本文来自微信公众号:autocarweekly (ID:autocarweekly),作者:七号-宋,原文标题:《汽车集成化和去集成化的博弈|技术流》,题图来自:视觉中国
大家有没有发现,最近很多有关的汽车领先科技新闻,都不约而同地提到了“集成化”这个词。
比如日前,哪吒汽车发布了浩智高效三合一增程器,具备了体积小、成本优、效率高、静谧性好的优点;特斯拉的后车架一体化设计也有“多米诺效应”,比如在今年,蔚来ES7已开始应用一体化压铸新技术;小鹏汽车则表示,未来将在武汉工厂建立新的一体化压铸工艺车间,同时引入超大型压铸岛及自动化生产线。
但与此同时,纵观汽车历史发展,也有不少零部件是从一个整体逐渐拆分为多个子部件。比如近几年大火的“滑板底盘+可拆分车身”概念,就旨在变革传统的车身模式,给到大家更全新的用车体验。
汽车到底是要拆解还是整合,这个决策让人难以抉择。
“化零为整”会是行业大趋势
“化零为整”的专业术语是“集成化”,它的目的是将许多零散的部分化为一个整体。
大家生活中已经遇到它了。新时代房屋和家具正在走集成化路线,它可以为我们带来更低成本支出、更少的搭建时间和更多的使用空间。
比如模块化房屋已经有起头之势。它是将房屋按功能模块进行拆解,先在工厂内完成加工,然后运到现场组装即可。以往数月才能完成的房屋,眨眼被压缩到数天。
汽车也是如此,就连汽车上极为庞大又复杂的零件——白车身,特斯拉也在想办法进行集成化。最早采用一体化压铸技术的车型是特斯拉旗下的Model Y,它的后车架本应该由70多个零部件由焊接方式拼接,但有了6000吨级意德拉Giga Press压铸机,后车架一气呵成,直接集成为一个超大零件,制造工序和时间被大大缩短。
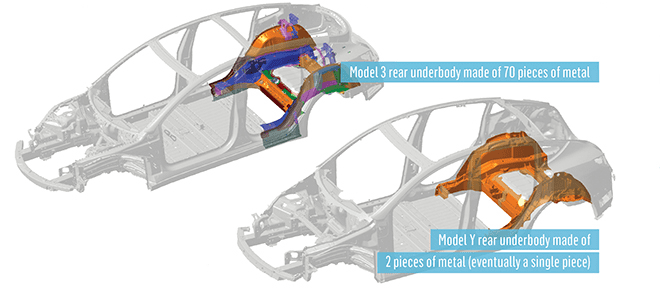
现在最新的电池包系统也在考虑使用CTP(Cell To PACK),它是将电池直接集成到电池包中,从而省去中间模组架构,简化电池包结构,提高空间利用率。手机产品也是类似趋势,现在基本都是电池机身一体化,能让电池和主板的贴合度更高。
特斯拉CTC方案异曲同工,只不过它是将车身地板作为电池包的上盖。这番操作下,MIT版4680 CTC Model Y的电池包(80kWh)+中控台+座椅+地毯总重仅544kg,要知道某款知名传统豪华纯电SUV,单80kWh电池包重量就达到了650kg。
总之,汽车行业也好,建筑行业也好,集成化设计可简化装配程序,提高产品合格率,还可以达到轻量化、节约成本等目的。
在汽车上,集成化在特殊部件上还能发挥特殊功效。电驱动系统的集成化设计可以实现驱动系统的轻量化和提升空间利用率。比亚迪集成化后的驱动总成、高压总成就比e平台1.0版的分布式结构减重了40kg,节省了一个大容量行李箱的空间(37L)。
而且将驱动电机与逆变器集成一体,逆变器配置在驱动电机旁,连接电机与逆变器的线束就可以缩短或者置换,也能减少线束因发热产生的电耗,妥妥的细节控。
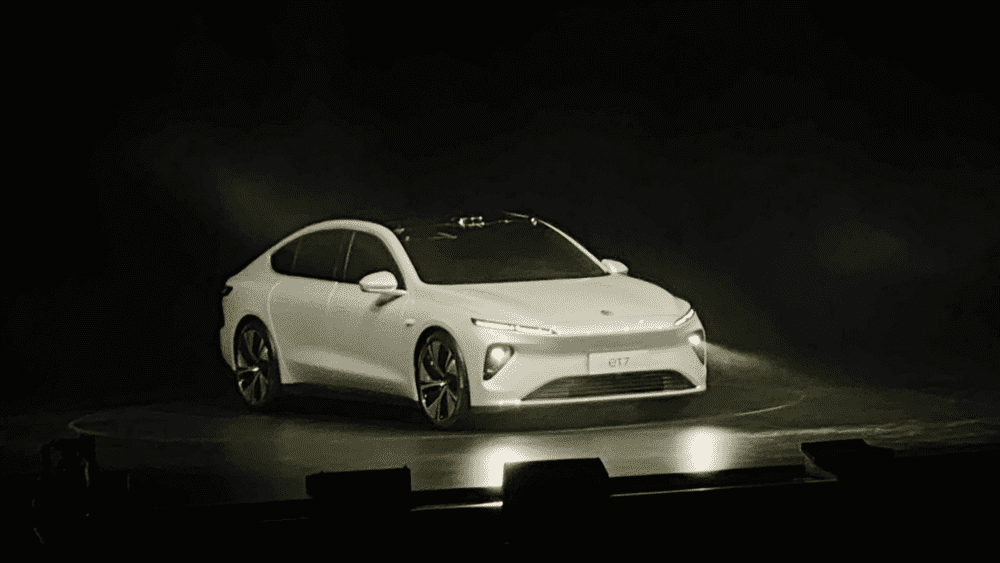
理想L9也采用了分体式前照灯组。理想ONE已经有将日间行车灯和大灯组分开设计的苗头,到L9身上,这二者的距离被彻底拉开,贯穿式LED日间行车灯被保留,其他灯被移动到前脸中部。
总结
零和博弈的结果是一方获利而另一方损失,且一方的所得正是另一方的所失,汽车集成化和去集成化还真有点像“零和博弈”。
大家当然更喜欢“双赢”的局面,但对于车企来说,汽车太复杂,这么庞大且集聚高科技的产品,要满足不同需求,就必须做出取舍。好在从消费者角度看,集成化和去集成化一起存在就是“双赢”,它综合了成本、效率、时间、性能、体验和美学需求。可以预见,这两种特征会同时存在于汽车中,直至汽车进化成最完美版本。
本文来自微信公众号:autocarweekly (ID:autocarweekly),作者:七号-宋