本文来自微信公众号:autocarweekly(ID:autocarweekly),作者:嗷嗷胡,头图来自:视觉中国
此时此刻,上海临港特斯拉工厂,超过660摄氏度的液态铝合金,在6000吨压力下被注入模具。几分钟之前是一摊铝水,几分钟之后模具打开,已经是一具成形的Model Y一体式后车身底板。
这是汽车历史上第一次,大规模批量生产如此尺寸的压铸铝合金部件。从2021年初至今,仅在中国特斯拉就已交付了超过13万辆Model Y,每一辆的后车身底板都是压铸一体成型的。
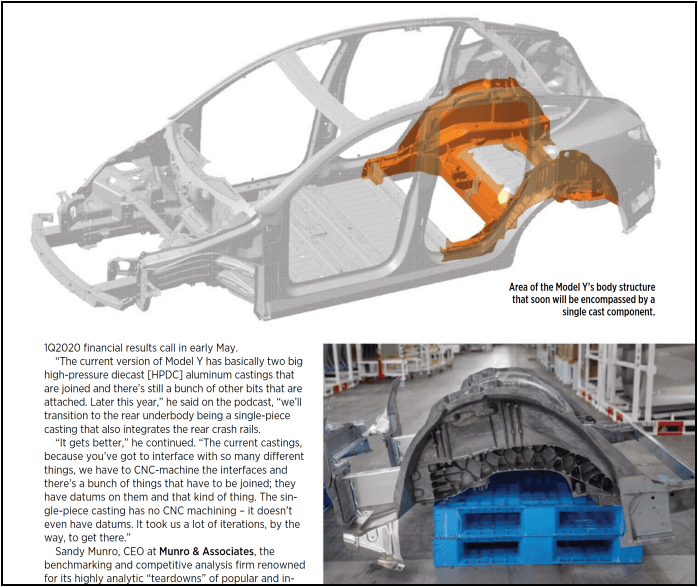
正在生产的Model Y只是个开始,去年特斯拉在电池日高调宣布了一系列新技术,其一便是压铸成型的前车身+后车身(目前只有后车身为压铸)。配合新的CTC电池包,整体可以实现减重10%、续航增加14%、减少370个零部件,不妨换算一下应用这些技术的新Model Y会有何等表现?
今年上半年,德克萨斯州的特斯拉工厂开始试制压铸前车身;不久后德国柏林生产的Model Y,将是拥有4680电芯、CTC电池包、前后压铸车身的“完全体”。
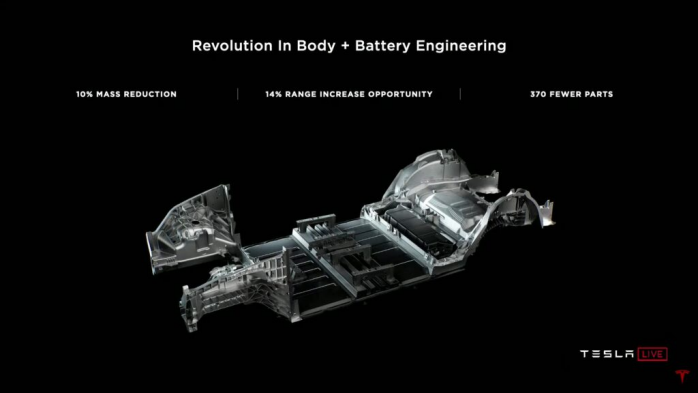
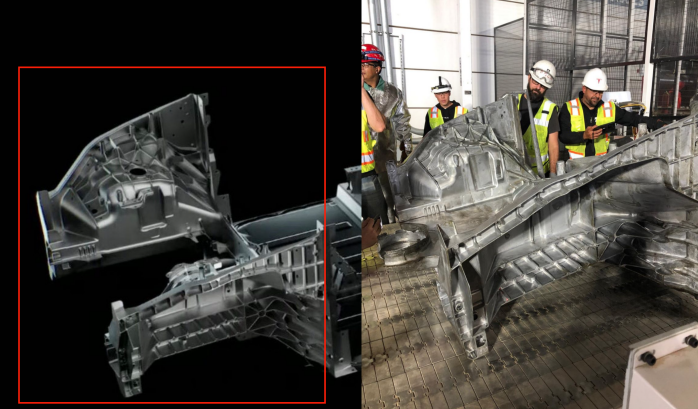
车身,或者说白车身结构(body in white),是直接定义一辆汽车“身份”与“使命”的关键和根本。这一点本胡天天睡觉做梦都在念叨,新来的朋友不妨跳转《为什么我一定要你关心“车壳子”?》。
部分车身采用压铸一体成型,好处在方方面面:生产效率更高、成本更低,车身重量更轻、刚度更高。落到俺们消费者身上,就是车价可以更便宜(只是“可以”,下同)、续航可以更长、舒适性可以更好、操控可以更强……
今天国产Model Y能卖到28万元起,可能就靠后车身采用一体压铸,成本省掉了那么几百几十几块几毛几——可千万别嫌少。要知道在主流民用车价位,多三位数人民币是足以让厂商打碎了牙往下咽的。
要明白压铸一体成型怎么个好法?我们得谈谈车身是怎么造出来的了。
从冲压焊接,到一体压铸
众所周知,车身的主要材质是金属。要将金属原料加工为车身部件,常规的做法是冲压成型。冲压,白话讲就是把金属板材放在预先设计好的模具上,挤压成模具规定的样子。跟月饼模子差不多,只不过这个“月饼”只有最上面的薄薄一层(板材)。
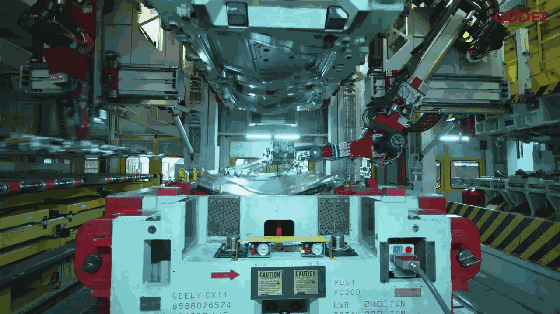
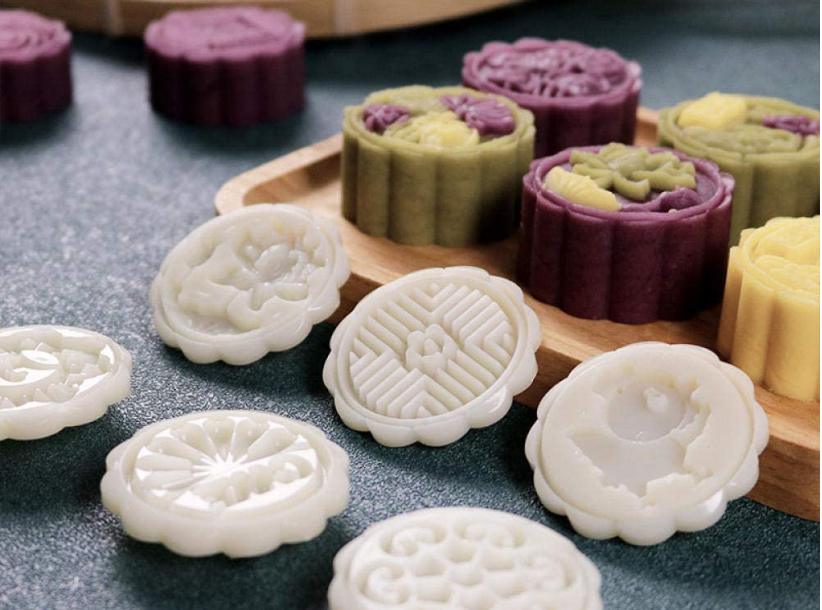
不过标题中的“压”并不是指冲压这个“压”。
无论多么复杂的冲压设计,部件终究是从板材(面)或型材(管)得到的,不大可能直接得到一个非常立体的结构——完整的车身可是一个大型立体框架。所以这些冲压件要进入到焊接车间,彼此“拼”成一整个车身。
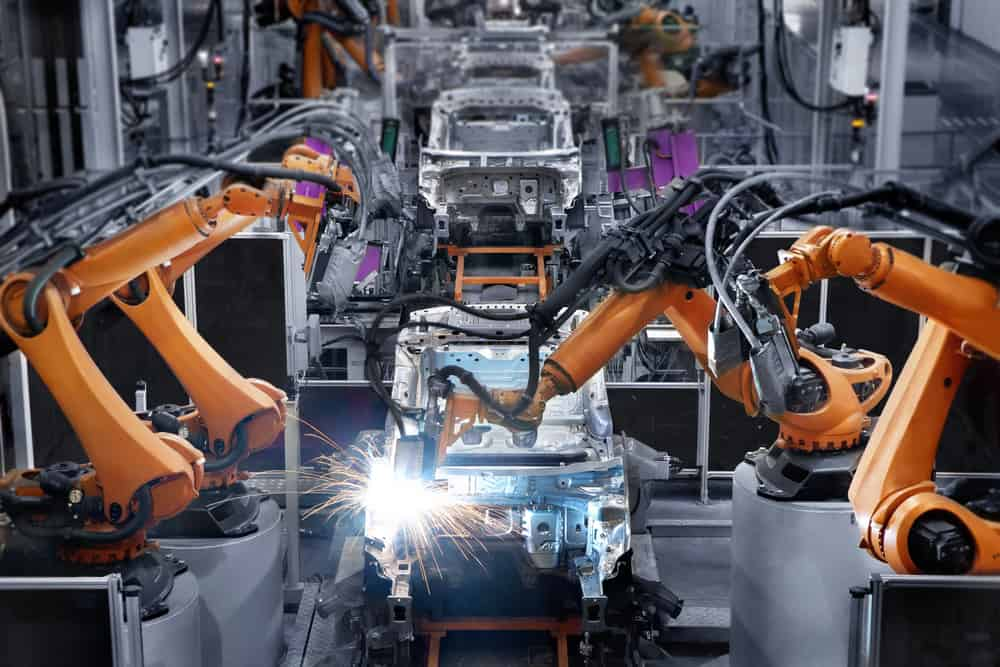
或者,还有另一种办法。
不直接利用金属原料,而是将金属加热到熔融状态,然后“趁热”将液态金属浇入模具中,等金属冷却固化,就得到了符合模具形状的零件,这就是铸造。压铸是铸造中的一类,靠高压强制驱动原料进入模具,可以用来制造较为复杂的精密零部件。
白话讲,就是把金属化成水,然后用“注射器”打进模具里,“放凉了”拿出来就是固态成品——基本原理就这么简单。因为是有动力挤压(压铸),所以模具可以做得复杂一些曲折一些,熔融金属依然能比较好地填充整个模具。
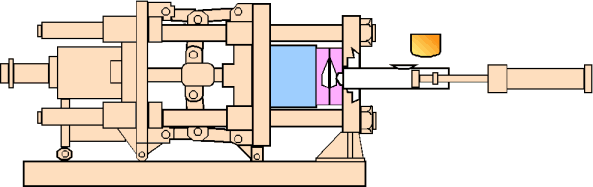
压铸其实常有
其实压铸并不是什么新玩意儿,甚至很可能你的车上就有压铸件——只是体积没有Model Y后车身这么巨大。
压铸能够一次制造出更复杂、更立体的部件,而不必先冲压再焊接(所以绝大多数时候“压铸”二字前后一定跟着“一体成型”)。因为这个特性,压铸特别适合制造大批量生产、同时又复杂不规则的零部件。
车身上有许多需要“不规则”的地方。传统的冲压工艺,只要是由一块钢板制成,无论被冲压扭曲成什么样,部件不同部位的厚度都是一致的。但有些地方需要高强度/刚度,有些地方又不需要那么高,即材料必然会有冗余。
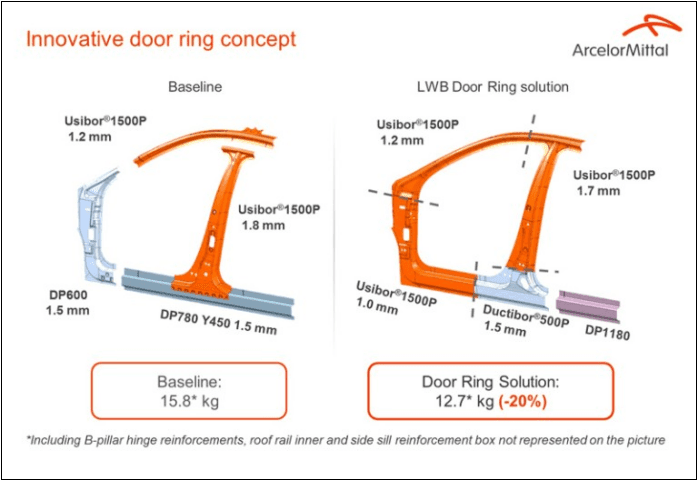
重量是永远的敌人。为了减少这种冗余,人们发明了TWB和TRB技术,可以一定程度上按照预设,使同一块钢板不同部位的料厚有所变化,从而实现“按需下料”。但这依然不够灵活自由,减重幅度和应用范围也有限。
真正的大杀器则是直接上铸铝,利用铸造模具的高度灵活性,预先为部件的各个部分设计好目标强度、分配好相应厚度(当然铝材本身也能减重)。不仅是不同部位的厚度可以自由变化,还可以设计特定方向的加强结构,“四两拨千斤”。如果采用普通板材,可能要高得多的重量才能达到设计目标。
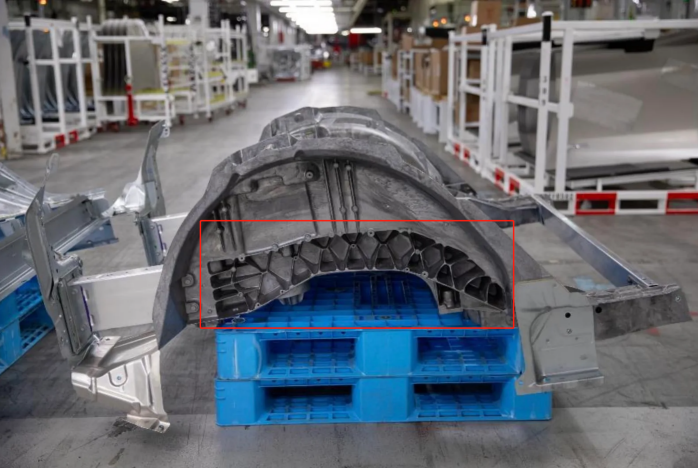
一直以来,车身上的铸铝广泛应用在悬架减振器塔顶。因为塔顶是路面应力传导到车身的最直接部位,需要极高的局部刚度,而形状又十分复杂。传统的塔顶由多个部件焊接而成,这本身就不利于减重,再要想达到高刚度,几乎必然需要极大的厚度/重量。
铸铝呢?一个部件就解决了,工序少而简单,重量轻且刚度大。
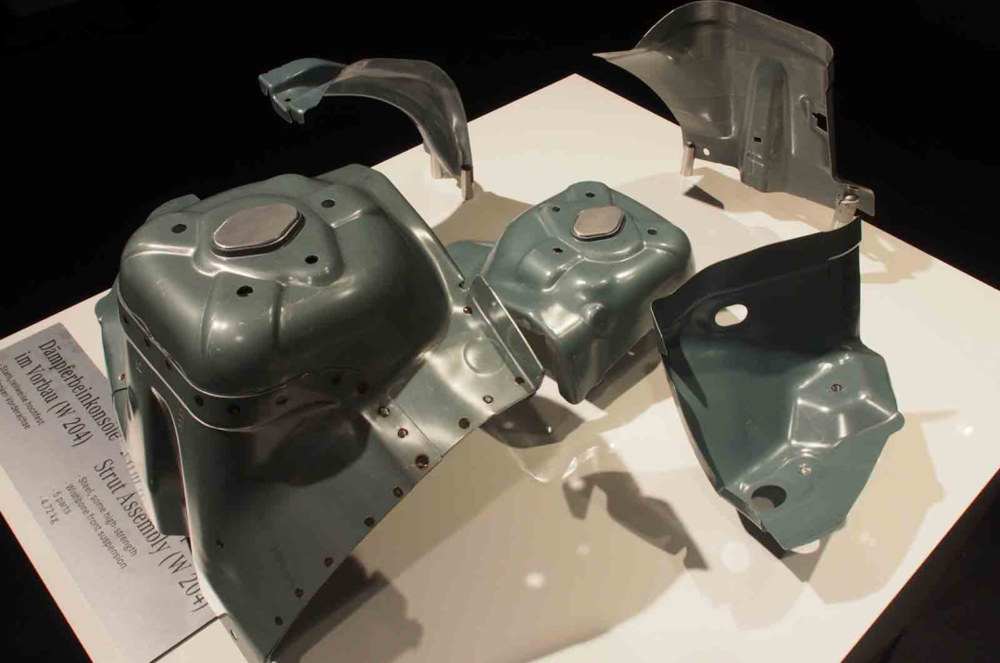
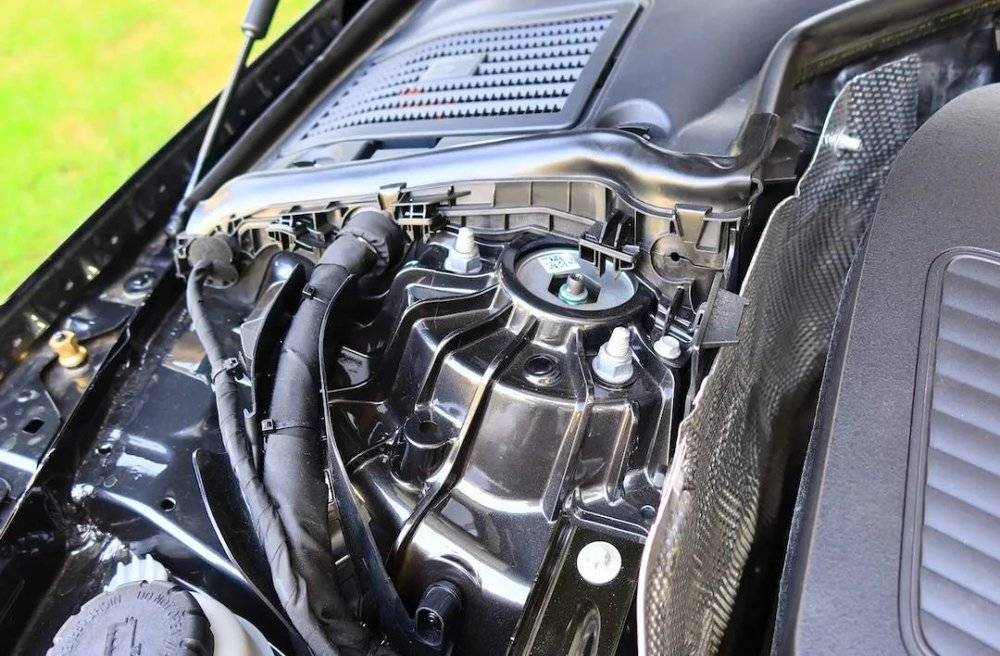
塔顶几乎是门槛最低的铸铝部件,目前在中型豪华车以上,铸铝塔顶几乎是标配。甚至零跑C11这样走廉价堆料路线的新造车,除了双叉臂前悬架,前塔顶也用上了铸铝。更大的铸铝部件则要到更高级别,此前提到奥迪A7为了减少掀背门对刚度损失,就在C柱顶端“关节”使用了铸铝件进行弥补(《掀背三厢车为何总是不入流?》)。
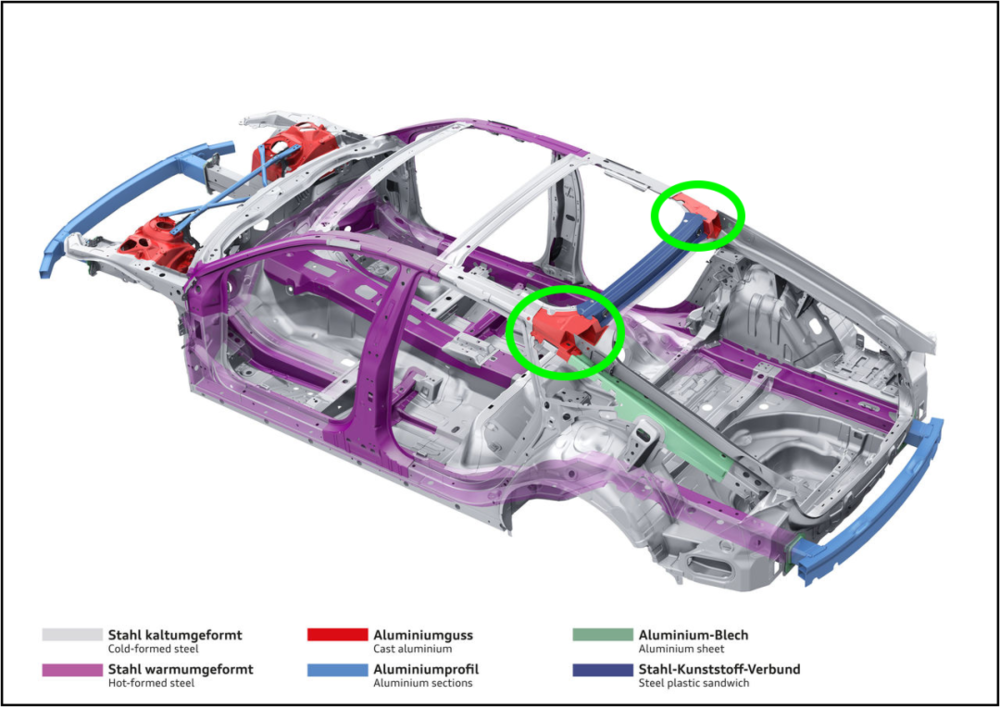
在Model Y之前,一体式铸铝工艺最大的部件,差不多就是车身的前后纵梁。这是凯迪拉克CT6的后车身纵梁,密密麻麻的加强筋体现出这是一个铸铝部件。
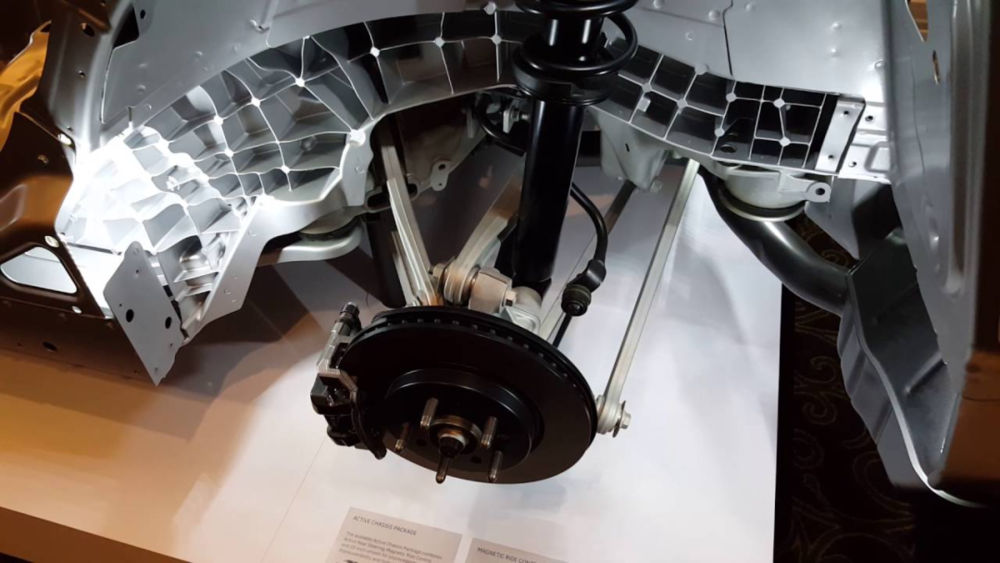
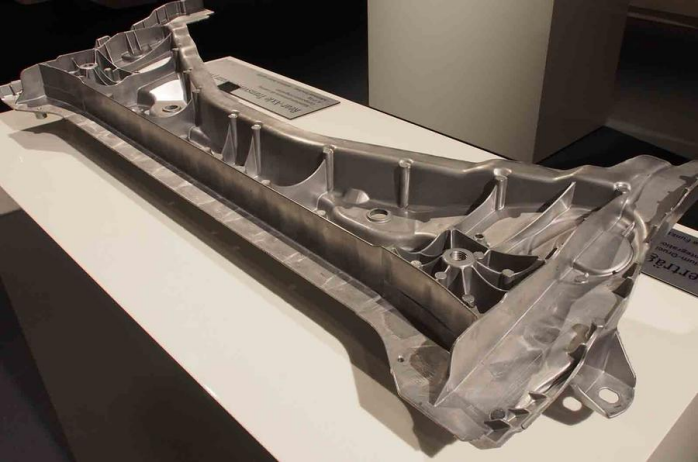
而大型铸件不常有
到了Model Y,特斯拉大笔一挥,将整个后车身底板、后轮拱、后横纵梁在内的一大部分,全部做成了一个铸铝件——这部分车身在Model 3上需要70个零件组成,更不要说柏林工厂后续的新版本,将前车身也做成了一体式铸铝件。
其实可想而知,大型铸铝部件直到今天才被特斯拉抢先应用,绝不是没有原因的。
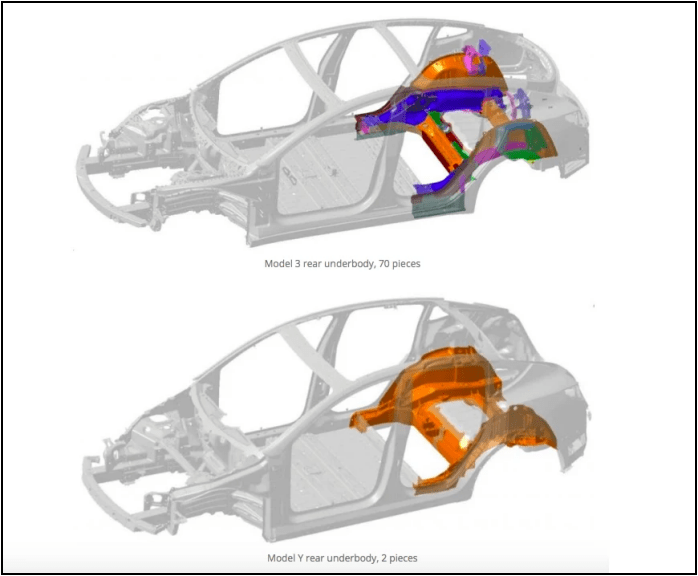
压铸工艺啥都好,一方面让零部件一体成型,减少了零部件数量和连接工序;另一方面铸铝实现了高度灵活的厚度和结构,轻松兼顾了轻量化与高刚度。但以往铸铝都是小部件,原因自然是铸铝件一旦体积做大,就会有难以解决的问题出现。
首先是需要更大的压铸机。特斯拉Model Y的后车身重大概80kg,这就需要压铸机能够一次性压入80kg的液态铝合金。只有当如此规模的压铸机被研制成熟,才可能制造这样大小的铸铝部件,目前世界上最大的压铸机可以一次性注入200kg原料。
柏林工厂Model Y的铸铝前车身,重量据说达到130kg,这意味着压铸机必须能够一次性压入130kg铝水。特斯拉之所以先上后铸铝车身(80kg),并且前铸铝部件是在全新的柏林和德克萨斯工厂率先启用,原因应该就是在等待更大的压铸机到位,并直接运抵新工厂。
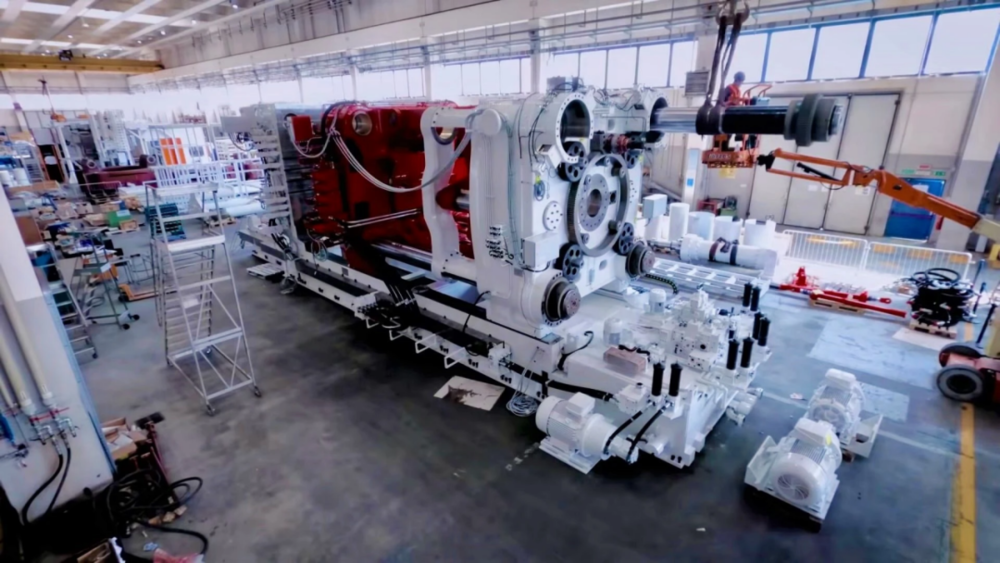
其次是铸造如此大的部件,本身就存在很大挑战。压铸原理看似简单,无非就是把液态金属压入模具嘛,但要想获得高质量的大型部件却问题重重,出品稳定的大型压铸机说是大国重器毫不夸张(上海工厂压铸机就来自国内的力劲集团)。
液态的金属并不“听话”,在被高压压入模具的过程中可能出现紊流、杂质等异常。越是复杂的部件/模具,越是容易发生填充不足之类的问题。模具中原有的气体和随料进入的气体,可能让部件内部存在气孔。部件缺陷时刻围绕着铸造过程,越是大体积部件可能出问题的地方越多,而汽车车身显然是容不得缺陷的。
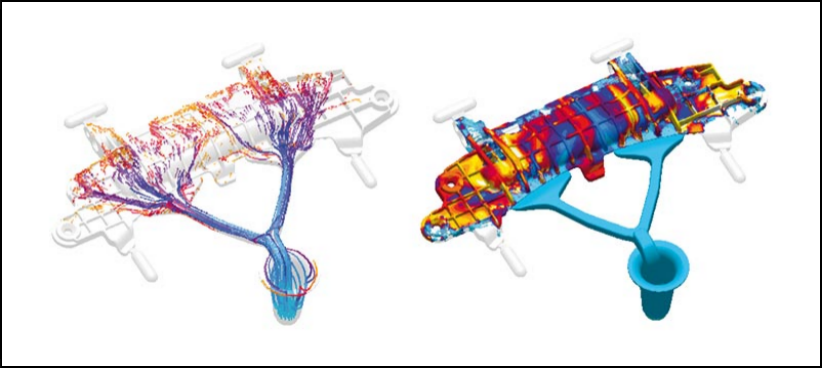
最后是大体积与高强度的矛盾。大体积的车身部件,更可能需要承担抵御碰撞的任务,也就更加需要高强度。但偏偏,一般铸铝件需经过热处理(固溶、时效,类似钢材中的淬火),才能获得高硬度高强度,而热处理必然带来热胀冷缩的体积变化,越是大体积部件,这个形变误差的影响就越大。
特斯拉最后是找到了一种无需热处理的特殊铝合金材质,才实现了Model Y的大型铸铝后车身。今年10月,蔚来宣布成功验证了可用于大型压铸件的免热处理材料,并将于第二代平台车型应用。找到无需热处理(潜台词是依然可满足强度需求)的材料,是大型压铸件应用的关键。
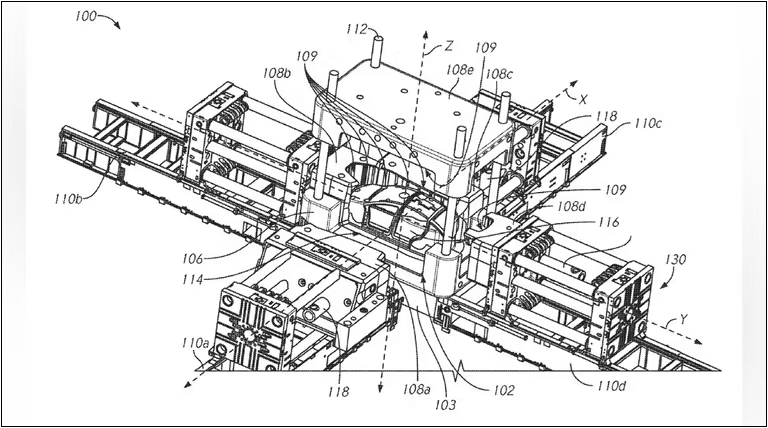
前后车身皆为压铸一体成型的Model Y还没真正量产,特斯拉早就在展望更远的未来。很早之前,特斯拉就提交过一个车身整体压铸的专利。
要知道上面所说的“后车身”,其实只是“后车身的一部分(当然,是比较关键的下半部分)”,终究还是要和其他车身部件连接。而特斯拉更加雄心勃勃的未来,是整个车身由单次压铸一体成型——真正实现字面意义上的“一步到位”。
这样科幻的一体压铸车身还很遥远,光是能容纳几百千克原料的压铸机就得些年头,更不要说如何设计这样复杂的模具、如何保证如此复杂的流场下不出现缺陷、如何确保整车压铸后拥有足够的强度等等。
其实车身部件的集成化、关键部件的铸铝化,一直都是汽车工业努力的方向。特斯拉作为搅局者,则是把一直滚动着的皮球向前踢远了一大截,自然也引来了很多追赶者。据说包括蔚来在内的几家车企已经在寻求大型铸铝件,当特斯拉逐渐靠一体铸铝获得更多优势,新造车企业对于产品力突破的饥渴,没准儿真会将这皮球踢得更快更远。
本文来自微信公众号:autocarweekly(ID:autocarweekly),作者:嗷嗷胡