本文来自微信公众号:我是科学家iScientist(ID:IamaScientist),作者:张浩,题图来自:视觉中国
不知从何时起,我们身边有越来越多的人开起了电动车,而最近,相信你也一定听到了很多关于电动车的新闻——“欧盟考虑2035年全面停产燃油车”“中国计划2035年将本土电动车销量占比提升至60%”,以及“特某拉电动车高速行驶着火”和“北京南四环一充电站起火爆炸”……
我们确实正在迈入电能源革命的新时代,但当我们不断眺望电能源利用的美好未来时,总不免担忧那一柄悬在我们头上的“达摩克里斯之剑”——锂离子电池的安全性。
为什么感觉近年锂离子电池爆炸事故频发?
无论是电动汽车还是储能电站,都离不开一种关键的器件——电池。几乎所有的电动汽车和七成以上的化学储能电站应用的都是锂离子电池,也就是我们手机和笔电中使用的这种电池。
由于锂离子电池出色地实现了电能源的便携化,助推了我们这个信息时代的发展。也因此,有三位对锂离子电池技术发展贡献最大的科学家获得了诺贝尔化学奖。
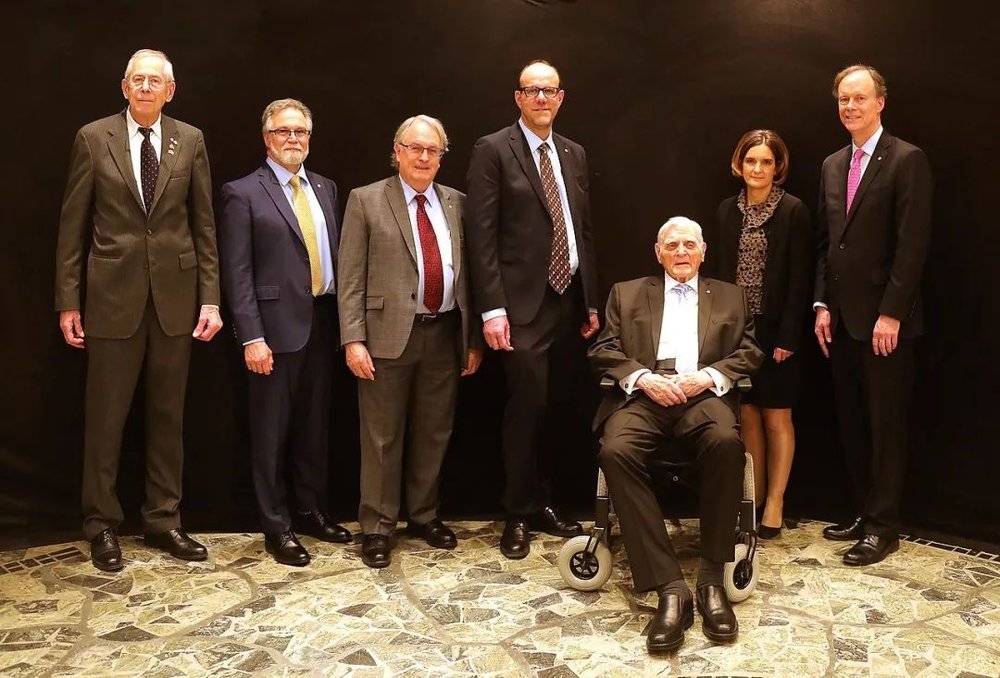
Flickr, US Embassy Sweden / CC BY-NC-SA 2.0(https://creativecommons.org/licenses/by-nc-sa/2.0/)
得益于锂离子电池的发展,其使用场景离我们非常近,我们的手机、相机和蓝牙耳机都需要它,但为什么应用到电动车上上、储能电站上,锂离子电池就发生了这么多事故?
这其实是一个概率的问题。比如某进口电动车所用的某进口电池号称事故概率仅为一千万分之一,但一辆车上要装8000支这种电池,相当于一千万支电池能够装1250辆电动汽车。也就是理论上1250辆电动汽车中,就有一辆车里的某支电池有可能会发生事故。若这个事故属于电池燃烧或者爆炸级别的事故,就有可能引发其周围的电池发生链式反应,进而造成电动汽车燃烧的大事故。
储能电站方面的事故也是如此,相比于一辆电动汽车大概能储存50~100度电,一个储能电池的集装箱体一般能储存1000度电,而一个中大型储能电站常常是几十个这种储能电池集装箱的集合。可想而知,这么大规模的电池用量,偶尔发生事故也很正常。另一方面,电动汽车与储能电站的燃烧、爆炸事故的后果显然要比手机电池严重太多,且目前的消防措施几乎对其无能为力。当然,我们也不能忽视这个消息传播如此迅速广泛的时代,那些时而造成人员伤亡的严重事件,便更容易造成较大的社会影响。
为什么锂离子电池会燃烧甚至爆炸?
锂离子电池是一种含能元器件,其主要由正极、负极、电解液和隔膜等组成。充电后其正极一般为过渡金属氧化物,其具有较强的氧化性;负极则为内部嵌入大量锂的石墨,有极强的还原性。电解液一般为有机酯类,具有熔点低、可燃等特点。
特别要注意的是,我们生活中的鞭炮也是一种含能器件,许多人知道其内含火药的成分为一硫(磺,化学式S)二硝(石,化学式KNO3)三木炭,其中硝石为强氧化剂,硫磺与木炭为还原剂,当外界给出一个超过120度的刺激后,鞭炮内氧化还原反应剧烈发生,释放大量气体与热量,火药燃烧、鞭炮爆炸。
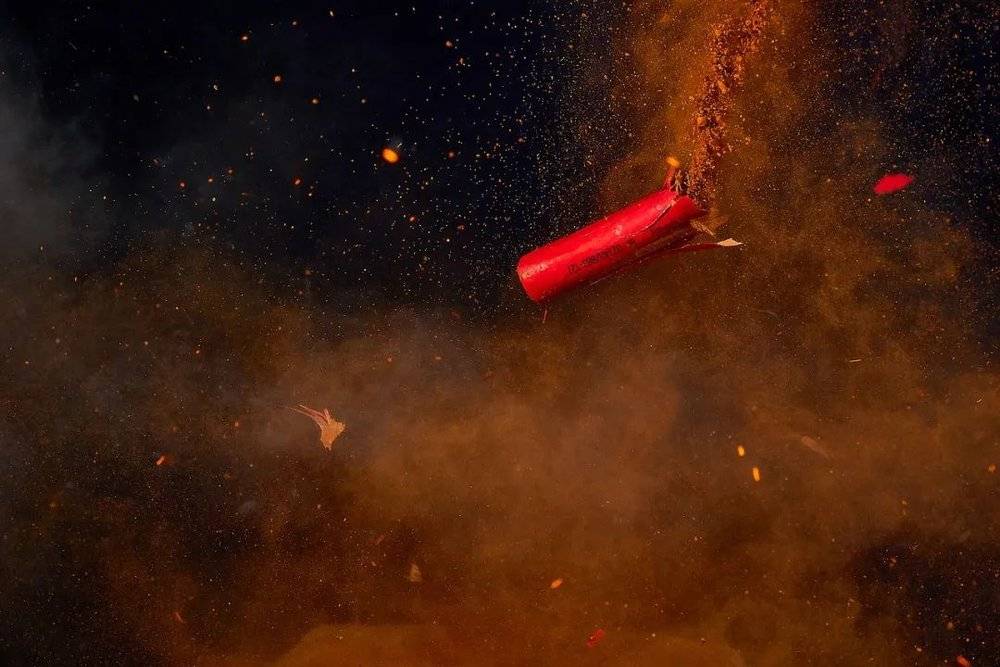
由此可见,理论上锂离子电池本征便可能发生高放热的氧化还原反应,且其内含的可燃电解液也会助推此反应,带来燃烧甚至爆炸的后果。锂离子电池燃烧或爆炸的威力有多大呢?光从其储存电能的角度来说,150Wh/kg能量密度的普通锂离子电池的电能大约是TNT炸药爆炸产生热量能量密度的1/10。
近年来的研究确凿地证明,锂离子电池事故中正负极在特殊情况下可直接发生剧烈氧化还原反应,甚至铝和铜集流体也能以还原剂的方式直接参与反应,产生的热量要显著高于电池储电对应的能量。一般来说,在密闭空间中锂离子电池发生安全事故,其最高温度能达到800℃以上,而一支43.4g重锂离子电池发生爆炸时的爆热相当于5.45gTNT,达到TNT当量的1/8 [2]。
而锂离子电池之所以不以剧烈的氧化还原反应而是以电化学反应的方式将其内部的化学能可控地、源源不断地转化为电能,是因为隔膜将正负极有效地物理隔离/电子传导绝缘(以及导离子电解液的存在)。但是,当出现各种内因或外因导致隔膜失效,进而正负极直接接触后,这种内短路会带来电能被瞬间释放,产生大量热并带来高温,瞬间破坏电池内部化学体系稳定,导致负极/电解液、正极/电解液、负极/正极之间,甚至集流体也参与的氧化还原反应,瞬时放热升温、造成电解液瞬间气化进而夹杂着负极/正极活性物质粉末喷出电池壳体,带来燃烧甚至爆炸的恶果,这个过程叫做热失控(简称TR)。
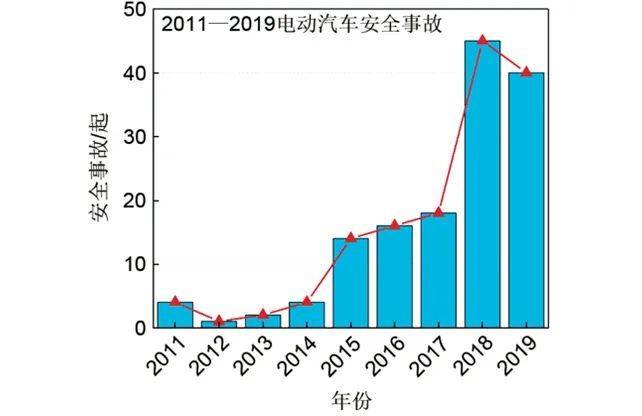
![滑动查看近年来电动汽车安全事故数量统计(左)与事故场景统计(右)| 参考文献<sup>[1]<br label=图片备注 class=text-img-note></sup>](https://i.aiapi.me/h/2021/08/19/Aug_19_2021_17_06_56_16391386391601851.png)
根据近年来电动汽车事故场景统计,大部分事故都是由于“自燃”,包括静置时(电池无充放电)、行驶时(电池放电)和充电时。少部分是有外部热源、碰撞和控制电路失效时发生的事故。
“自燃”属于自发性热失控,后者统称为各种滥用条件下(热滥用、机械滥用、电滥用)的热失控。尽管两类情景下热失控最终带来的升温、燃烧等机制相似,对其展开研究的难易程度却有很大的差别。目前,滥用条件下的热失控由于激发条件可控,近年来研究取得很大进展,基本能够定量描述各种滥用条件激发热失控的机制及随后的危害情况。但自发式热失控,由于其诱因复杂不好预测,热失控后的电池又被完全破坏很难复原热失控前的微观状况,成为研究难点。
为什么难以预测锂离子电池热失控?
自发式的热失控是目前电动汽车最大的安全焦虑。为什么其难以预防?这都要从电池的制造说起。
如果每一支电池从微观的电极材料颗粒、隔膜到宏观的极片、壳体封装都100.000000000%的完全一致,那用几千个或几十万个这种电池做成的电池组肯定会有更好的安全特性。你可能注意到这里百分之百的表达方式有点不一样,后面有十来个零,这代表着一种理想的预期——电池全尺度的高一致性。
众所周知,电池不一致性的后果就是性能劣化的电池会更快地衰变,有些钝化失活,直接失效;也有部分走向了另一条截然不同的道路——内短路进而热失控、燃烧、爆炸。
那这种危害最大的自发式内短路为啥就不能预测呢?
原因主要一是这个衰变到内短路过程十分缓慢且外界电压信号不明显,二是出事的电池都直接在几分钟内直接进入破坏式的热失控,电池全毁,证据无法回溯,也使得此领域研究进展缓慢。
真正精确模拟自发式内短路的过程,目前仍是一个难题。另外,电池类似一个黑箱,尽管我们能用一些电化学谱学和原位CT的技术手段从外部监控个别电池的电化学反应与内部微观结构变化,但我们无法预测数千万支电池中哪支会在数个月或数年后“猝死”并对其全生命周期的演变进行细致研究。每一支电池刚出厂时都几乎绝无自发性热失控风险,但哪支在半年后或三年后的某个夏夜或冬晨“猝死”并造成大规模燃烧事故?现在很难预测。
这像不像我们人体?
电池原料参数与制造工艺类似我们的基因,电池充放电制度如同我们的饮食习惯,电池使用环境温度变化如同生长环境。随着成长,总有一些人的身体中会产生长期炎症或者更严重的血管病变,进而在短期有可能发展成癌症或造成卒中,这就类似电池内短路及随后的热失控。
如果我们能有能力对地球上每个人24h的健康状态进行实时监控,那我们就能够尽早发现异常并进行处置,减少癌症与卒中风险,但这显然不符实际。同样,我们也难以承担对每一块电池进行最全面的实时监控,现在大致能对数十块电池组成的一个模组装配监控电压和整体温度的装置,而这离研究与预防电池单体自发性热失控的要求显然差距甚远。
能够确定的一点是,提高电池的一致性能提高电池组的安全性和可靠性。然而,完美的一致不可能做到,单说电池正/负极活性物质的颗粒,其每一个的形状、表面状态、缺陷等特征,只要放到分辨率足够高的设备下都能看出差别。除了原料,电池制备还涉及数十步复杂的工序,想让电池保持一致非常困难。尽管现在动力电池产业投资动辄数亿就是为了获得更高的加工精度,但锂离子电池众多的原料和复杂的制备工序使得一致性的提升成为一项永无止境的任务。
电动汽车当然还会继续发展,我国也将继续推广大规模储电技术在能源体系中的应用。根据我国能源结构现状,电动汽车在我国中长期能源战略与未来可持续发展具有重要重要地位。相信随着电池技术体系的持续高速发展,未来5-10年,其可靠性与安全性必将显著提升。
但是,完全杜绝锂离子电池的燃烧事故,几乎是不可能的。
![通过痕量氢气探测提前预警锂离子电池热失控示意图 | 参考文献[4]](https://i.aiapi.me/h/2021/08/19/Aug_19_2021_17_07_00_16391391155375014.jpeg)
当然,在尊重客观现实的情况下,还有很多提升安全性的工作可以展开。首先是创新的预警技术,比如斯坦福大学近期报道对氢气信号的灵敏捕捉能把预警锂离子电池热失控的时间前推5分钟,这足够电动汽车上的人员逃生的了。另外,电池的自毒化技术也比较有效,其机制是当电池发生热失控的前期,能够释放出一些特殊化学物质使得电池内部钝化“瘫痪”,打断了热失控的链条。
正视锂离子电池安全性,大力发展创新高效的安全性提升技术,持续提升电池制造一致性。总有一天,这类“爆炸”性新闻,将不再在我们生活中出现,我们可以安心地使用电动车。
参考文献
[1]冯旭宁,等.电动汽车事故致灾机理及调查方法,储能科学与技术,2021,10,544.
[2]王青松,等.密闭空间中锂离子电池的热爆炸安全性,储能科学与技术,2018,7,424.
[3]Fachao Jiang, et al. Questions and Answers Relating to Lithium-Ion Battery Safety Issues. Cell Reports Physical Science, 2021, 2, 100285.
[4]Yi Cui, et al. Detection of Micro-Scale Li Dendrite via H2 Gas Capture for Early Safety Warning.Joule, 2020, 4, 1714.
[5]王莉,等.锂离子电池安全事故:安全性问题,还是可靠性问题,储能科学与技术,2021,10,1.
本文来自微信公众号:我是科学家iScientist(ID:IamaScientist),作者:张浩