根据2019年的统计,刨除停摆项目,中国大陆共有57座芯片制造工厂在建或者已经投入使用,这些项目总投资额度超过15000亿人民币。
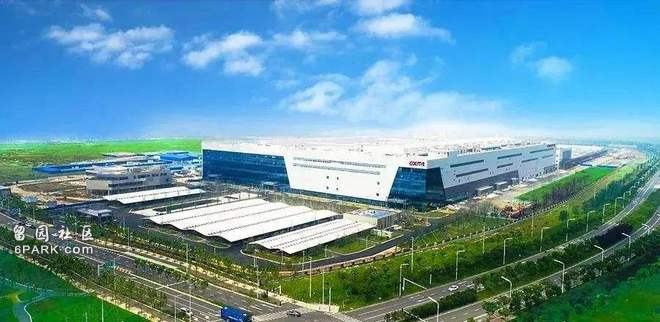
(图为位于合肥市空港经济示范区的长鑫存储DRAM芯片厂,有望打破国外企业的垄断)
规划与建造任何一个芯片生产线都是极其浩大的工程,建造之后良率爬坡过程同样难上加难。那么,它到底难在哪里呢?
(一)当我们建设芯片厂时,究竟在造什么?
首先,一个完整的芯片工厂厂区,要包括但不局限于如下空间配置:
中央供应设备厂房、主要生产厂房、生产辅助厂房、厂务区、办公区域。中央供应设备厂房:包括电气室、发电机室、污水处理室等。主要生产厂房:包括无尘生产线、送风区、回风区等。生产辅助厂房:仓库、清洗塔区等。厂务区:气体存储区、化学品存储区等。
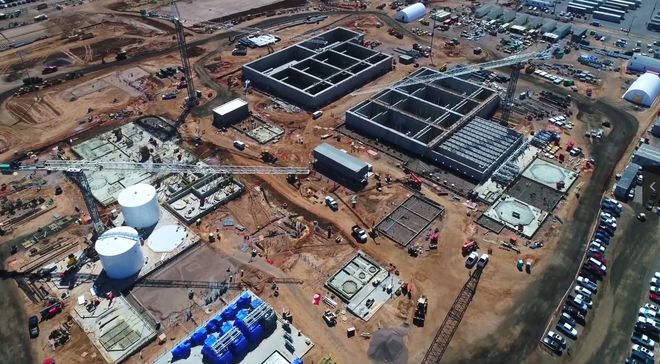
(某芯片工厂建设施工现场,分为上述多个区域)
这其中,最重要的就是主要生产厂房的无尘生产线,又名无尘室、洁净室,工程师们称其为fab(英文词fabrication的简称),在这个空间中分布的是各式各样昂贵的设备,如动辄几亿美元的光刻机。
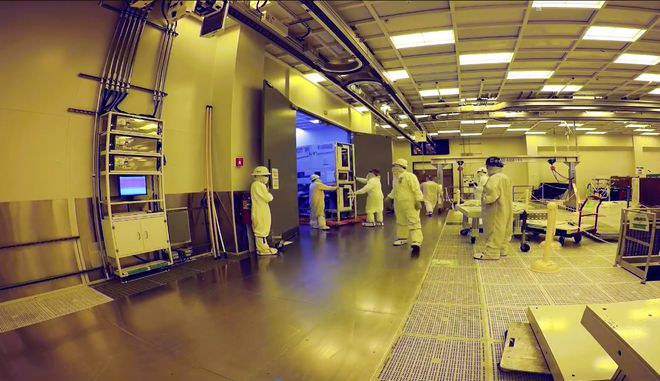
(某芯片制造新厂,大型设备进场)
在fab里,芯片的前体-晶圆-以FOUP(前开式晶圆传送盒)为单位经过天车系统在不同的设备之间穿梭。取决于芯片的种类,每一片晶圆要经过几百至上千步不等的加工工艺才能成为可用的成品。
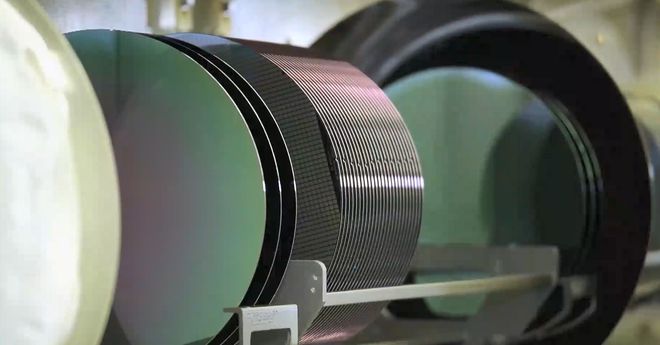
(一片晶圆可以分割为成百至上千颗芯片,图为正在进入炉管工艺的晶圆)
在典型的建筑厂房设计中,无尘室处于整个建筑的三层,一层与二层是附属、辅助性的区域,包括附属机台的维修室、气柜、电柜、化学品供应管路、厂务设施主系统管路等。四层设计为房顶梁柱与空调系统。
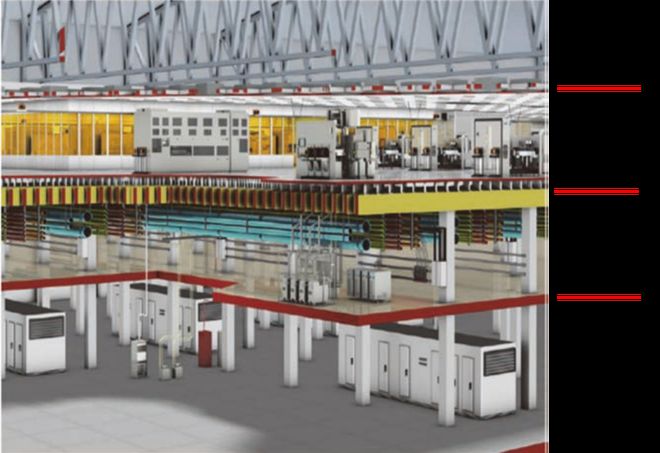
(芯片制造主厂房剖面图)
在无尘室中,所有生产人员需要穿着特制的无尘服,以抑制人体活动产生的皮屑、油脂、飞沫、毛发、化妆品、衣物纤维等污染物与微颗粒。
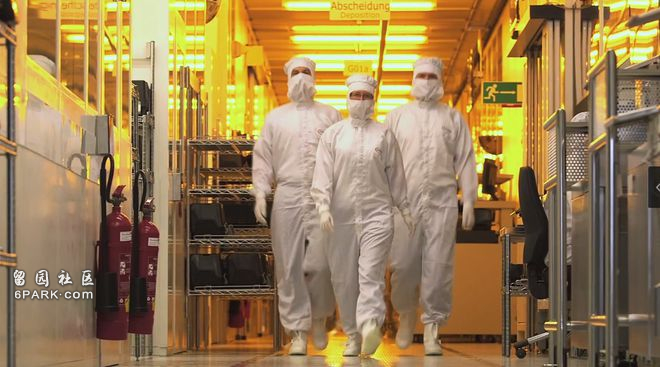
(生产线上身穿防尘服的工作人员)
代表无尘室干净程度的指标是单位体积空气含有的微颗粒的数量,这有着严格的国际标准。老式的标准是Federal Standard 209E,它的衡量标准是每立方英尺中0.5微米以及更大颗粒的总数量,例如,一个10000级的无尘室,代表了每立方英尺中,0.5微米以及更大尺寸微颗粒的总数量不超过10000颗。2001年以后,这个标准被ISO 14644-1标准所取代。该标准考虑了更小尺寸的微颗粒,给予了更精确的衡量标准。
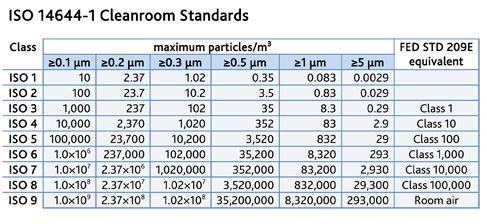
(Federal Standard 209E与ISO 14644-1标准中的无尘室等级对应关系)
除了空气,无尘室还要保证温度、湿度常年几乎恒定。为什么环境条件要维持得如此苛刻?这是因为芯片的结构超级精细,一个晶体管的尺寸尺度在纳米与微米级别,同样尺度的微颗粒落在晶圆的表面,就会造成微观结构完整性的破坏,进而造成器件失效。而温度与湿度的剧烈变化,则会造成不恒定的微观化学环境,进而造成光刻、氧化等过程的工艺偏差,同样也会造成电路失效。
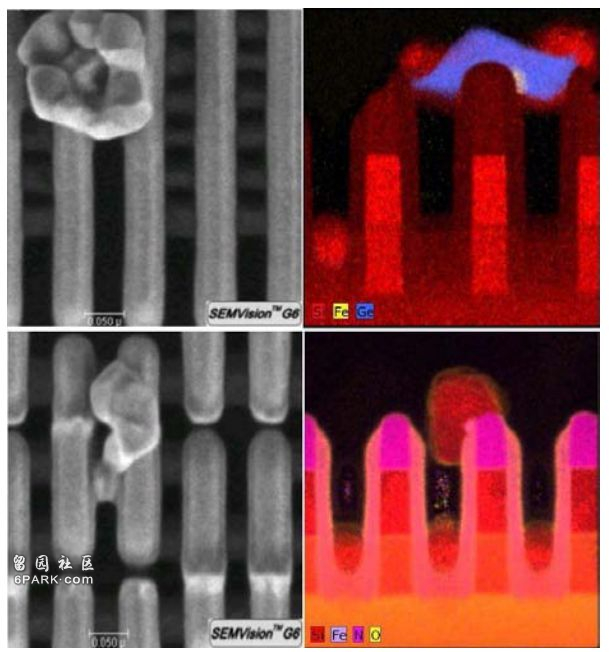
(因外部颗粒引起的芯片微观缺陷)
(二)万事俱备只欠东风:良率爬坡冲刺的难题
如果新厂建设过程中没有出现投资方撤资、施工方跑路、企业被某霸权国家制裁等幺蛾子事件,那么恭喜,这个新厂已经成功了一半——但这距离能生产出合格的产品依然有着很远的距离。
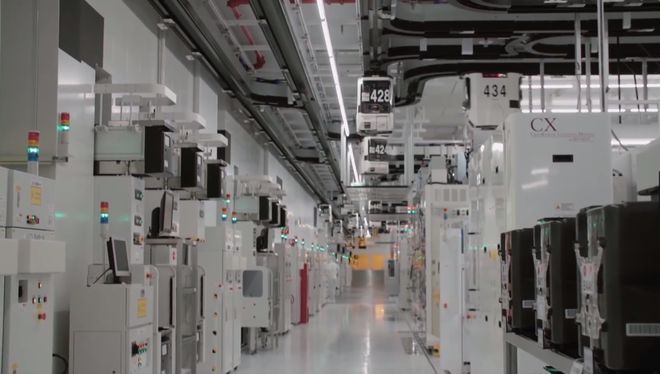
(建成后的无尘室,整齐排列的设备)
工程师们首先要确定工艺流程步骤和每一步工艺采用的工艺参数。如果新厂使用的技术细节是搬运自自己的其他工厂,则这个过程就会大大简化。比如我国著名芯片代工厂中芯国际,后建的北京fab厂制造同一类型的产品,在工艺流程与工艺参数上就会大体上搬运已有的上海fab厂的相应内容。
值得说明的是,有现成技术可以“搬运”并不代表万事大吉,因为在很多步骤上,即便新厂与母厂的工艺参数设置完全一致,也经常会出现得到的工艺效果并不一致的情况。这主要是因为芯片制造的工艺要求极其精密,工艺效果的制约因素极其众多,实际的工作中很难做到这么多工艺参数与母厂完全一致。另外,还有很多未知的因素才起作用。所以,很多时候,工程师就要因地制宜地对工艺进行不断地调整。
对于半导体产业的新入局者,上一过程则要经历得更为漫长。比如长江存储,它是一个2016年才成立的半导体“新人”,并没有现成的成熟生产线来提供可以照抄的模板,所有的技术细节都要自己摸索。
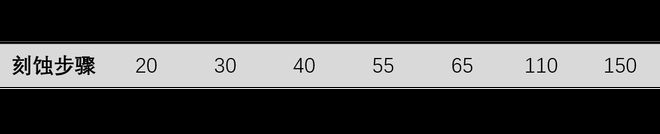
(一般来讲,芯片越先进,工艺步骤越繁琐,近年来的先进芯片的全流程步骤超过1000步)
工艺研发团队首先要根据芯片的物理结构给出可行的制造方案。这需要新厂投入大量的实验性流片。研发团队通过不断的探索,需要掌握每一步的工艺窗口、工艺弱点、工艺失效模型等信息。
研发工艺阶段之后仅仅是确定了芯片制造流程的大体框架,验证了芯片的可制造性。此时的良率还很低,产线依旧处于亏损状态。
下面介绍一下什么是良率。以晶圆级良率为例,在一片晶圆完成了所有的工艺步骤之后,在切割成单个芯片之前,要进行包含成百上千种电性测试的测试环节。最终判定为合格的芯片占总测试芯片的比例就是良率。
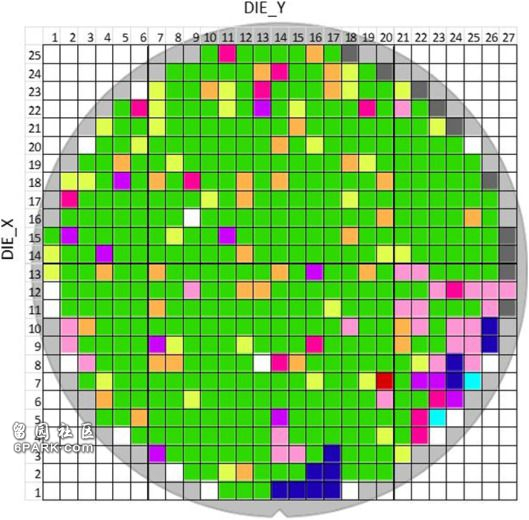
(晶圆良率测试结果图举例,假定绿色代表通过良率测试,其他颜色代表因各种原因电性失效)
当研发团队将相应工艺细节转给量产团队之后,量产团队针对每一步的工艺细节的常见失效问题进行不断的优化。排除那些造成失效的工艺因素,才能使得良率逐步提升。通常情况下,良率爬坡到稳定阶段通常要1-2年的时间。
良率稳定在高水准之后就万事大吉了吗?并不是。这之后,要通过严格的管控与科学的监测保证没有工艺事故的发生。多数工艺事故来源于人为错误、原料供应与设备故障等。单在原料供应上,芯片制造厂就要承担大量的风险。芯片制造需要使用大量的多批次原料,包括各式各样的气体、固体、液体和特殊化学品。很难保证供应商提供的各批次原料中一直没有不合格产品的存在。即便是质量管控强如台积电这样的大厂,也发生过因供应商化学品批次质量问题导致的大量产品报废事故。
结语
总体而言,把一个芯片制造工厂从建设到投入运营并最终维持稳定盈利,是一个高技术、高投资、长周期、高风险的行为。所涉及的技术面之广之精密,都是其他制造业不可比拟的。大国要崛起,掌握芯片制造尖端科技已经是大势所趋。我国在芯片制造领域虽然已经积累了相当的经验,但离最先进的水平相比还有一段距离,为了弥合这个差距,芯片人正在努力。
参考文献与资料:
[1] 庄子寿,半导体产业经济规模及其厂房设施概论[J].土木水利,2019,46(06):4-12
[2] 吴心玫. 半导体厂房空间之研究─以厂务设施为例[D].中华大学,2008.
[3] https://www.portafab.com/what-is-a-cleanroom.html