虽然这十年来,我们有些企业一直在努力攻克这项技术,但是事与愿违,我们并没有实现国产化,所以这些年,我们一直在高价购买铝塑膜。
它有多贵呢?我们拿电池隔膜做对比,同样是电池的五大材料,它的单价比电池隔膜贵很多,2020年时,两者相差10-20倍,2021年时,这个数据就变成了20-30倍。
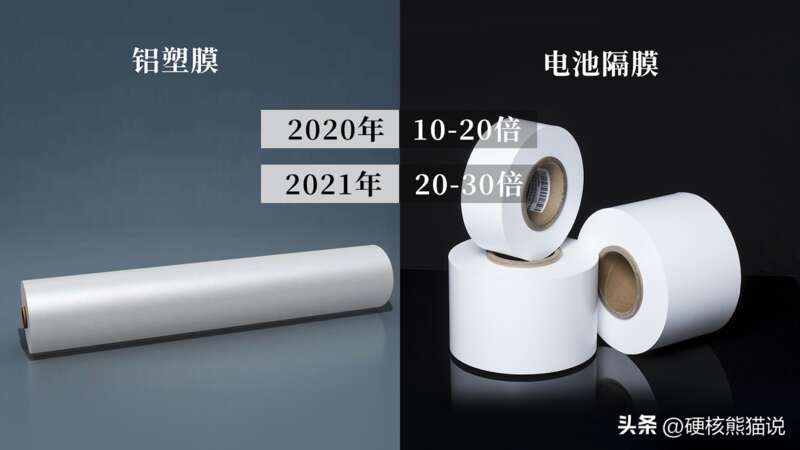
很明显落后就要挨打,而且别人还是不知轻重地下死手。但是这还没完,即使是同等品质的铝塑膜,国产的也要比进口的要低30%左右。
双重价格差距的背后,其实就是国产铝塑膜技术和产业话语权丧失的痛苦。
所以有很多中国企业拼了命的也要攻下这块高地,他们花费巨资,饱和式地布局铝塑膜,用业内人士的话说:产能肯定超出了,但是此时此刻,不是考虑产能过剩时候,而是考虑在电池拐点来临之前,能否解决卡脖子的问题。
这个拐点就是下代电池技术,因为铝塑膜已经确定是下一代电池,固态电池的核心技术,如果还不能突破这项技术,我们锂电池产业多年的努力和市场成果,将会大打折扣,甚至还会处于被动当中。
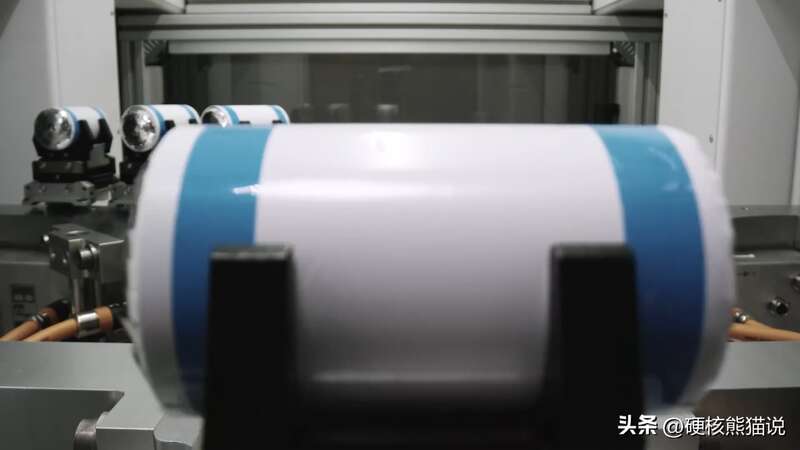
那么问题来了:铝塑膜到底是啥,既然它这么重要,为啥就它没有国产化?我们能突围成功吗?
大家好呀,我是熊猫,今天咱们就来说说,中国锂电池最后的攻坚战。
被中国弯道抛弃的技术:铝塑膜
铝塑膜严格意义来说是被中美同时抛弃的技术,不过世事难料,它又重新被重视起来,这里面还涉及到赛道之争、封锁中国与中美弯道超车的曲折故事,这个故事还要从铝塑膜的发展说起。
锂电池有三种形态,分别是圆柱、方形和软包电池,这三者的结构其实都差不多,但是电池外壳的封装工艺却相差得比较大。
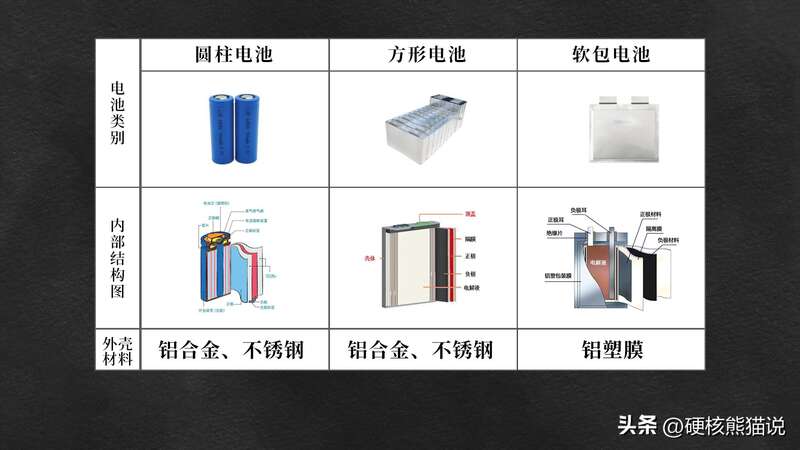
圆柱形电池和方形电池的包装材料采用的是铝或者钢作为外壳,所以比较硬,而软包电池的外包装采用的就是铝塑膜,它的厚度不到1mm,所以很薄,也很柔软,用它制成的电池有尺寸和型状可调节等功能,所以又叫软包电池。
那么中国铝塑膜是如何被卡脖子的呢?这就要说到铝塑膜的发展和结构了。
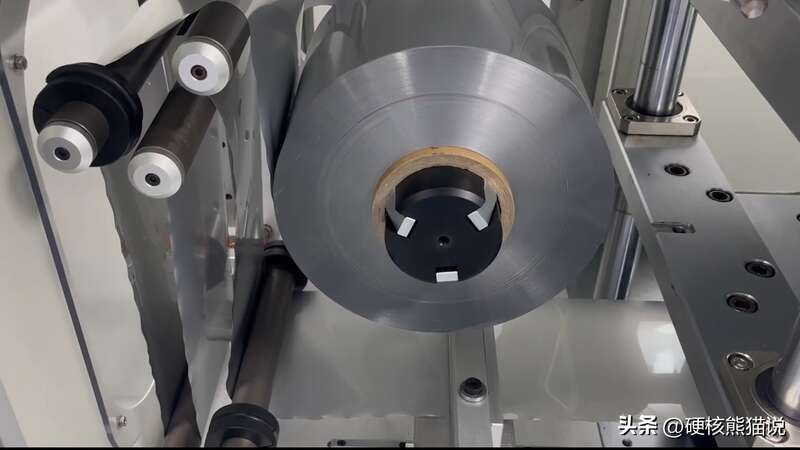
铝塑膜的诞生得比较晚,在1998年时,由日本索尼和昭和电工联合研发,不过它们生产的铝塑膜主要是给索尼固态电池用的,结构中用了多层接着剂,接着剂会和电解液反应,导致铝塑膜不耐受,影响了液态电池的寿命。
所以第一代铝塑膜的性质并不是很优秀,2001年,日本昭和又推出第二代铝塑膜,但是依然没有改变这个方案,所以除了索尼外,有很多品牌也感到很头疼。
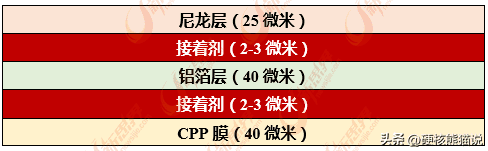
不过这个问题,很快就被日本其他企业改正了,同样是在2001年,DNP与尼桑公司开始联合研发生产铝塑膜。
他们改进了昭和电工的工艺,在他们的基础上,用酸性材料(MPP)替换了接着剂,铝塑膜的抗电解能力就变强了,于是DNP很快就获得了软包电池企业的认可。
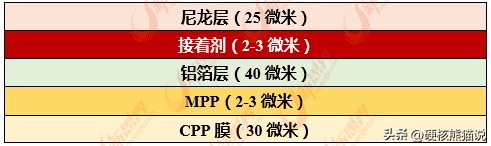
DNP将铝塑膜发扬光大后,其他国家也开始学习日本,研制自己的铝塑膜,尤其是韩国,他们在数码产品等3C消费电池上有技术、产业和产能的优势,然后他们将这种优势复制到汽车的动力电池上,由此发展出许多优秀的动力电池企业。
尤其是LG,他们财大气粗,在锂电池上跑马圈地,很快就抢占大量份额,并且成为软包电池领域的领头羊,对于下游的铝塑膜行业有很大的话语权,韩国企业也借此对铝塑膜进行了布局,并且很快取得了成功。
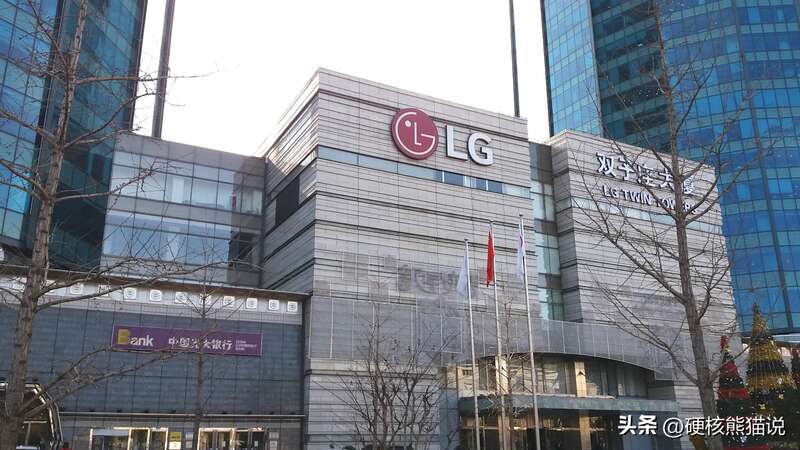
铝塑膜的市场很快就被日韩垄断,当然这里面的大头还是日本,但是不管怎么说,日韩联合起来,长期把持着铝塑膜产业链上下游的话语权。
相比之下,中国铝塑膜虽然关注比较早,在1997年就有试着生产铝塑膜,不过也是抱着尝试的态度,直到2001年,中国将电动车列为863计划重大技术专项,电池的零部件才受到资本的重视,国内也有企业开始布局软包电池和铝塑膜。
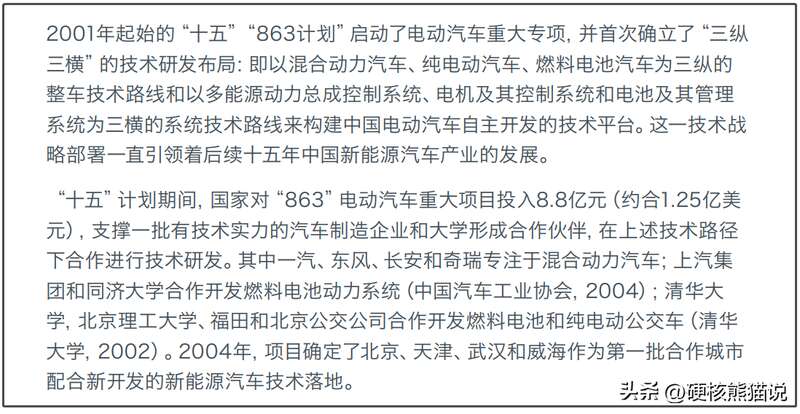
于是日韩对中国铝塑膜长久的技术封锁和垄断就开始了。
国产铝塑膜被日韩封锁:进退两难
先说下日本。
他们在2001年后就进入中国,但是为了防止铝塑膜的技术外泄,从不在日韩以外的地方设厂,尤其是中国,他们在国内采用的是代销模式,利用中国的代理商进行售卖,这样做虽然能保护技术不外泄,但是对中国的软包电池企业却非常不友好。
因为多了一层中间商,所以铝塑膜的成本就会高很多,加上他们并没有把控代销商的资质,谁能帮他们卖货,谁就可以代理,导致中间商数量众多,而且良莠不齐,为了竞争就得压低价格,然后又以次充好谋取利润,让我们的电池企业苦不堪言。
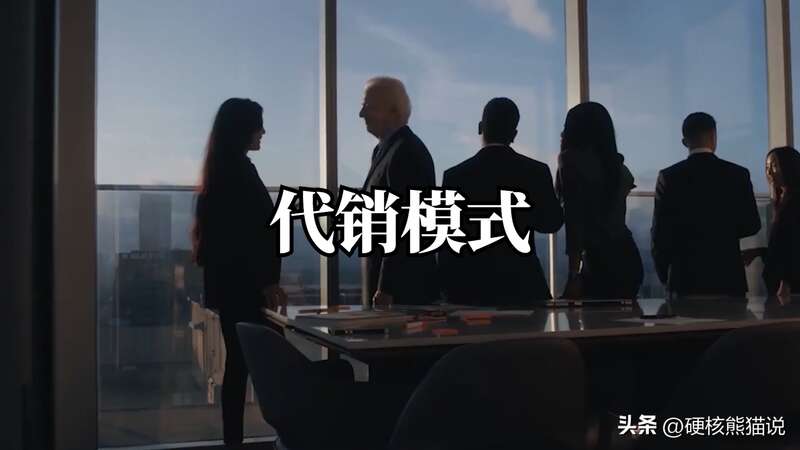
这还没完,铝塑膜的市场空间并不大,只有几十亿元,而日本的铝塑膜企业大部分是跨国企业,他们业务和资金都很雄厚,压根看不上这块小小的市场,所以故意控制铝塑的膜产能和价格,谋取更高的利润。
这种做法让中美欧等软包电池企业非常被动,不花高价购买,就要被限制供货,于是有很多企业瞄准这个赛道,其中也有中国的企业。
2004年,国内软包巨头紫江公司注意到铝塑膜市场,他们经过市场调研后,决定对铝塑膜尝试公关,紫江公司原本从事的是包装领域,常年给可口可乐生产包装瓶,对包装用的铝塑复合膜技术积累非常丰厚,所以在他们看来,攻克材料相近的铝塑膜并不是什么难事。
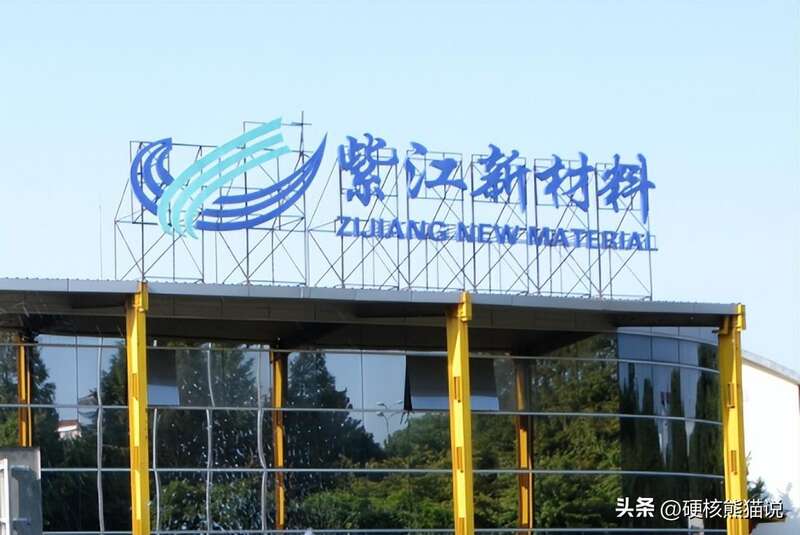
于是他们在2004年成立了一支专业铝塑膜研发团队,不仅网罗了相关的人才,而且将自己积累的工艺和经验都用在铝塑膜生产线上,果然在7个月后他们就拿出了国内首批国产铝塑膜。
可惜的是紫江低估了铝塑膜的难度,因为铝塑膜要包裹在电池外表面,而且要保护好电池的正负极和电解液等组件,所以铝塑膜就需要具备比较强的物理和化学性能,比如:阻隔性,耐穿刺性、绝缘性和耐腐蚀性等等特点,还需兼顾强度和韧性。
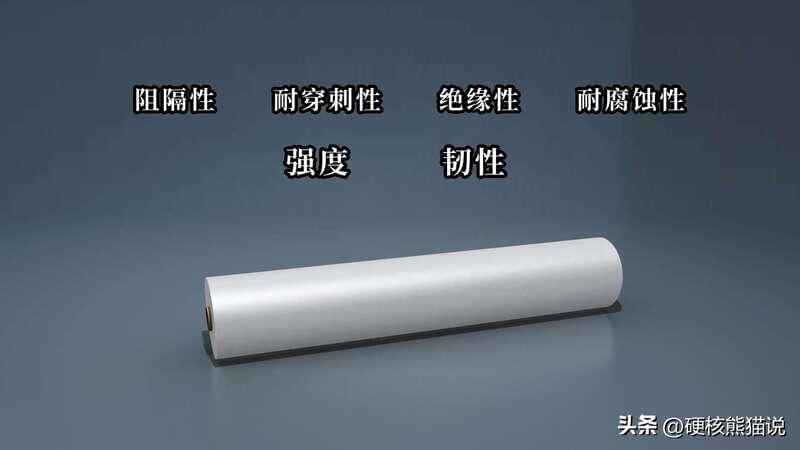
这些特性有些是矛盾的,导致它看起来就是一层膜,好像技术难度并不高,但是真正生产出来了,就会发现某些性能达不到要求,紫江生产的首批铝塑膜也是如此。
他们在生产出来的时候,就将产品送往了广州数家工厂进行测试,结果有很多性能都无法满足要求,不过紫江并没有放弃,他们将自己包装材料挣得钱,源源不断投入到铝塑膜中,对技术和工艺进行攻关,产品质量逐步提升。
2009年,紫江研发的第二代铝塑膜,获得了市场的认可,很多中低端企业开始采用紫江生产的铝塑膜,具备了独立成长的能力。
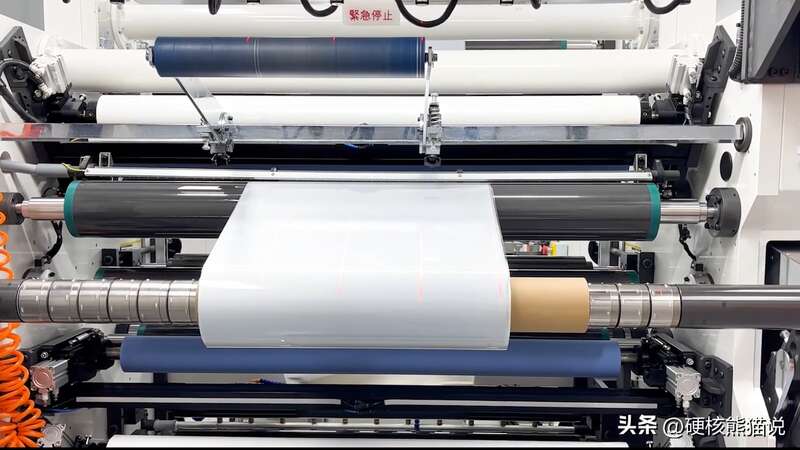
2012年为了更好地发展铝塑膜,他们还专门成立了:紫江新材料公司,专门负责铝塑膜的生产和销售,2年后,他们攻克了第三代铝塑膜,这次他们终于敲开了高端铝塑膜的大门,先后成为全球锂电池巨头ATL、三星、万马等企业的供应商。
国产铝塑膜逐渐走上正轨,而且在紫江之后,国内还有很多铝塑膜企业正在发力,并且逐渐站稳脚跟:比如新纶、明冠新材、卓越等。
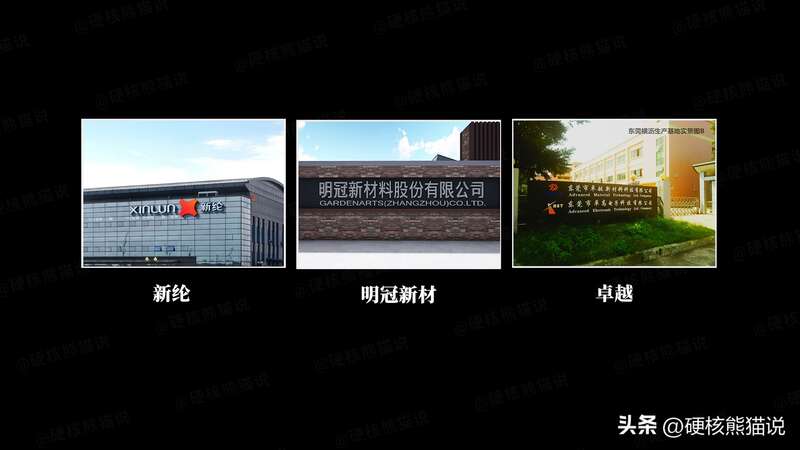
但我们的铝塑膜企业依旧受到很大的质疑,因为铝塑膜的下游软包电池大部分都掌握在韩国手里,尤其是韩国的LG等企业,掌握了大部分软包电池的专利和技术,他们不仅不用中国生产的铝塑膜,还联合日韩企业对中国动力电池的展开一场倾销战。
国产锂电池危机:日韩联合绞杀,工信部悍然出击。
2015年时,我国新能源汽车经过多年的补贴和培养,终于跃居为全球第一市场,然后这个时候,日韩企业却瞄准了我们的胜利果实,LG、三星、日本松下等企业同时对中国的动力电池打起了价格战。
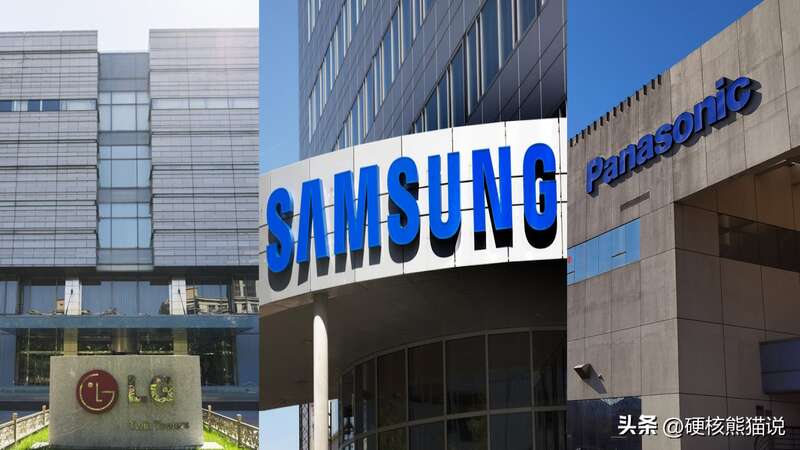
他们一边扩大产能,一边压低动力电池的价格,宁愿自己亏损,也要抢占中国的市场份额,这是典型的“搞死对手,再独占市场”策略,当时的中国电池企业还在积累当中,面对国际巨头的倾销根本无力抵抗。
日韩企业很快以中国电池一半的价格抢占了大部分的市场,中国锂电池企业们面临前所未有的黑暗。
要知道新能源汽车中成本最高的就是电池,可以占到35%以上,如果中国锂电池企业倒下了,那么下一步可能就是中国的整车车企们,也就是说日韩企业的目的就要窃取我们多年培养的市场。
这种情况下,我们当然不会坐视不理,2015年3月,为了保护中国电池产业,工信部发布了《汽车动力蓄电池行业规范条件》,也就是大名鼎鼎的“白名单”,对于搞乱市场,不符合规范的企业不再进行补贴,而倾销战的主力韩国LG就被阻挡在名单之外。
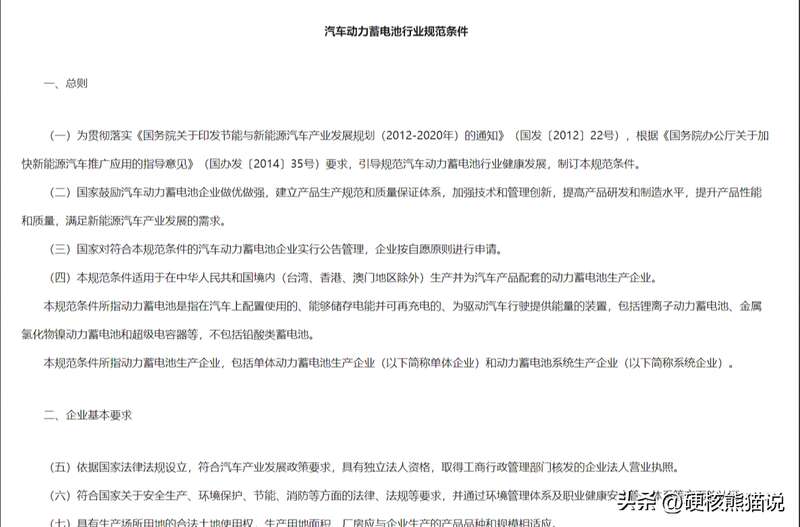
中国动力电池也借此迎来了大翻盘,但是铝塑膜和软包电池却因此失去了市场份额。
因为LG公司拥有大量的软包电池专利,加上软包电池价格贵、技术要求高等缺点也很明显,
中国动力电池自然不会再选择这个路线,而是朝着圆形和方形电池研发。
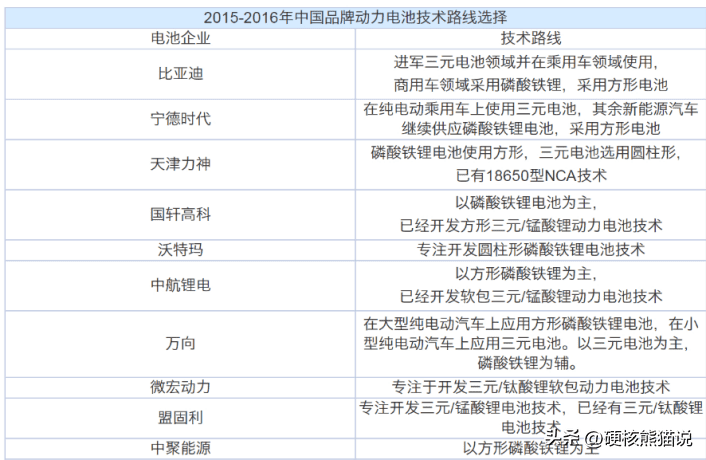
而在中国之外,情况也差不多。
日本掌握铝塑膜的话语权,但在2010年后,他们选择了氢能赛道,对于铝塑膜的扩产并没有兴趣,只想着搞钱和给韩国企业供货,而韩国软包电池企业又非常短视,把软包电池专利当做倾销工具。
而且软包电池也有自身的缺陷,它除了价格贵外,软包电池的一致性非常差,因为它使用的铝塑膜是柔软的,用它来包裹电池,电池很容易就会改变形状,没办法做到统一的规格,当然也不是没办法解决,比如重新套上一层壳,但这样价格就更高了。除此之外,软包电池还容易鼓胀,防刺破、工艺要求过高等特点。
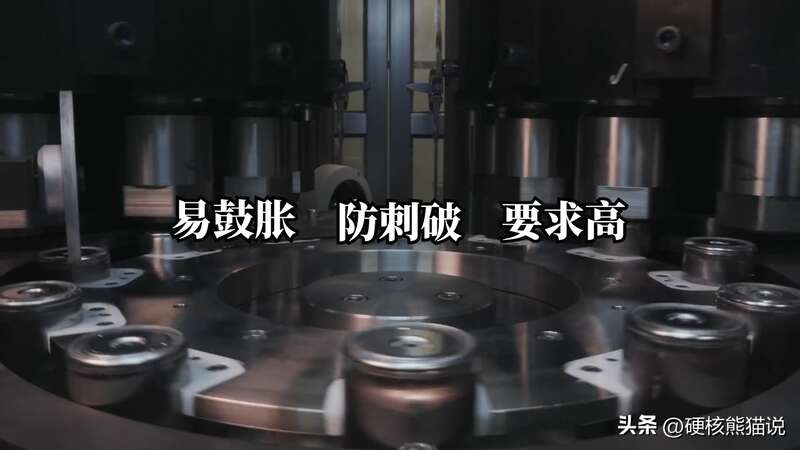
马斯克甚至公开吐槽过软包电池,并且建议其他公司也不要使用它们。
所以中美欧的电池企业不愿意再被日韩卡住脖子,突破起来又困难,干脆就同时抛弃了软包动力电池,改走其他路线。
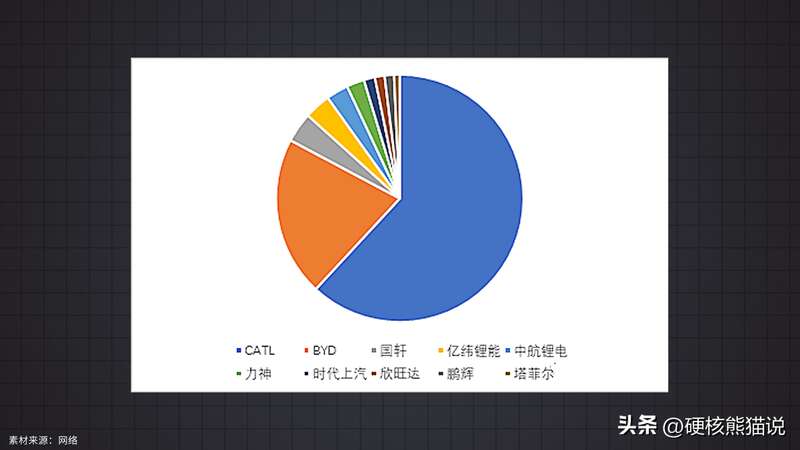
其中宁德时代和比亚迪同时选择方形电池,并且推出CTP技术和刀片电池,将方形电池做成市场主流路线,占据80%的市场份额。
而特斯拉选择了技术更加成熟的圆形电池,并且研发出了4680电池,也占据了一席之地,唯独软包电池,在日韩的反向努力下,逐渐走向了没落。
2019年时,国内软包动力电池的份额下降到5.5%,作为软包电池的上游,国产铝塑膜企业几乎是躺输,大部分企业面临着亏损的境地,即使是紫江新材料的业绩也在不断下降。
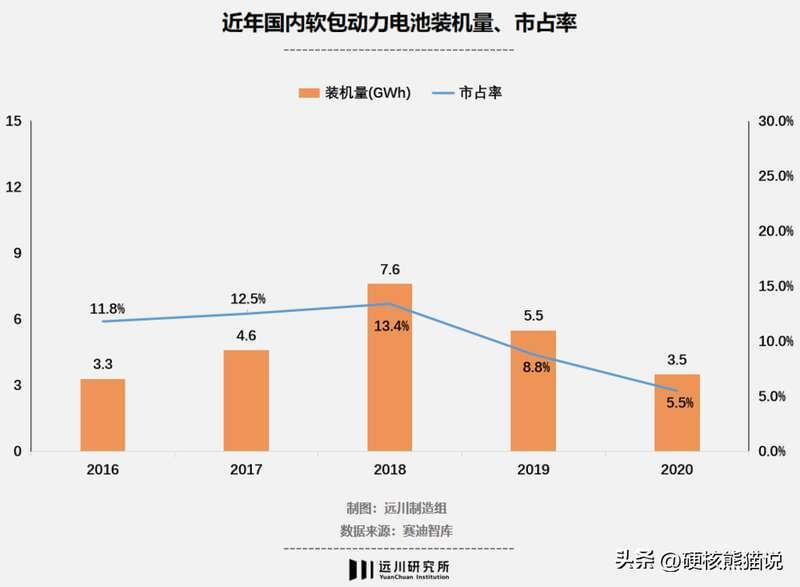
所以中国为啥没有实现铝塑膜国产化,是有历史因素的,铝塑膜本身的市场小,又是被中美同时淘汰的技术,自然不会有太多精力花费在它的身上。
当然看到这边,有些人会说:既然铝塑膜曾被中国淘汰了,现在又为何会成为卡住我们脖子的技术呢?
铝塑膜:命运中绕不过去的坎
这里的故事比较狗血了,就不得不说下固态电池和铝塑膜的优点了。
我们都知道,现在锂离子电池的能量密度已经做到了极致,所以很多企业都在备战下一代电池,而下一 代电池有固态锂电池、钠离子电池等等分支,其中固态锂电池最适合的形态就是软包电池。
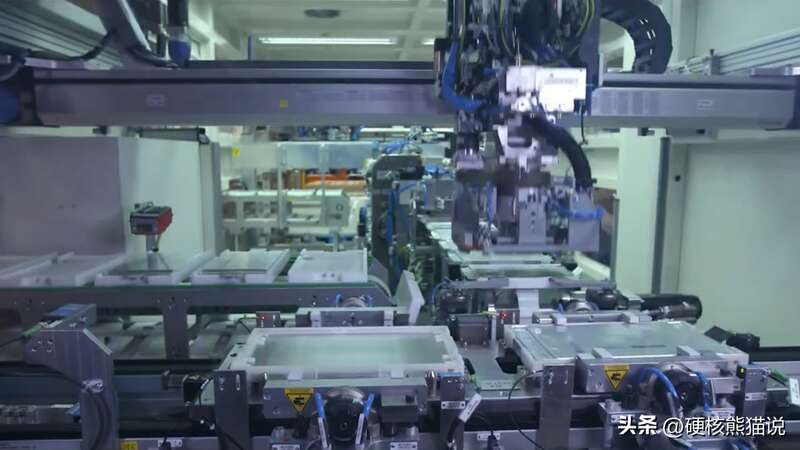
圆形和方形电池的外包装都是比较硬的金属材质,圆形是将它卷绕成圆柱状,方形是通过卷绕或者叠片成方块,而固态锂电池内部的电解质是固态的,不能卷绕,最好的方式也是一层层叠起来。
但是软包电池的铝塑膜非常薄,厚度只有微米级别,用它叠出来的固态电池能量密度比方形电池更高,除此之外,铝塑膜的内阻更小,臌胀时还可以通过排气来增加安全性,所以软包电池和铝塑膜就成为固态电池中非常重要的一条路线。
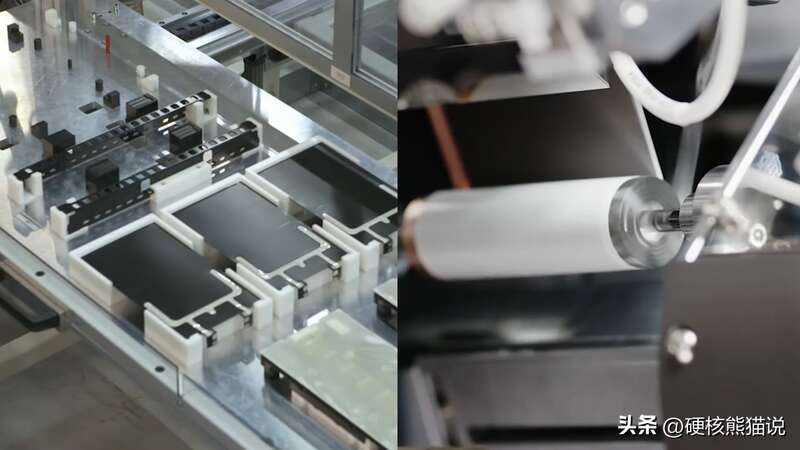
说白了,技术变革就是这么巧妙,铝塑膜,这个原本卡住我们脖子,然后被我们弯道超车的技术,却在下个时代,神奇般地重新拦在了我们面前,而且市场依然被日韩掌握在手里。
那么问题来了:既然它变得这么重要,那么我们的企业还会被卡脖子吗?
答案肯定是不会的,虽然在市场份额上,日韩依旧占据了70%,但是在技术上,早已发生了天翻地覆的变化。
在铝塑膜行业衰退的那些年,我们有一些企业一直在坚持和成长,他们在没有政策支持的情况下,依然坚守着这个领域。
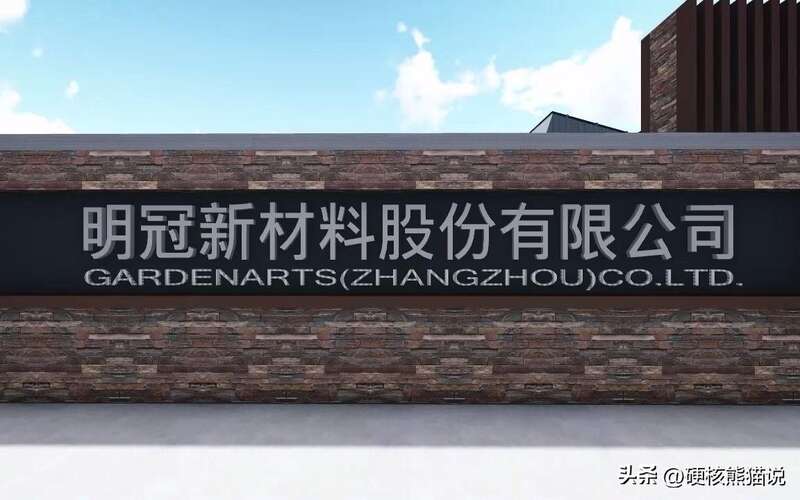
当时铝塑膜虽然败走动力电池,但是在3C消费电池、2轮摩托车等小市场上还是依然有需求的,日韩企业不愿意扩产,而且比较高傲,订单不是拖延,就是不想配合,每次订货都要3-6个月,效率非常慢。
我们国产企业则不一样,他们甚至愿意用农村包围城市的战略,靠着这些小蛋糕,一步步成长起来,不管是技术还是工艺都已经达到世界前列。
以技术为例:
铝塑膜传统的工艺有两种,一种是以日本昭和电工为主的干法工艺,还有一种是以日本DNP为主的热法工艺,这两种各有优缺点,难度也都很高,但是中国企业却也都一一攻克了,
典型的例子就是上面说的紫江新材料,他们在攻克热法铝塑膜后,就开始逐渐取得客户的信任,先后成为全球锂电池巨头ATL、三星、万马等企业的供应商。
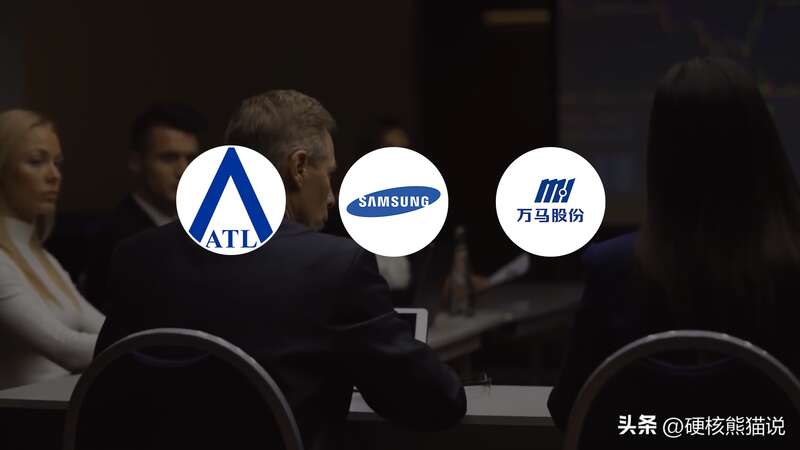
在国际上,铝塑膜每月出货量能达到百万平米级别的热法铝塑膜企业有2家,其中一家是行业龙头,日本DNP,还有一家就是中国的紫江新材料,时至今日,紫江的铝塑膜出货量已经达到世界前三。
除此之外还有明冠新材料,他们结合干法和湿法的工艺优势,自己开发出一种新的复合方式,从而实现了全产业链的自主创新。
明冠新材总经理在一次交流会上详细讲解了他们的六大专利技术,凭借着这些专利,明冠成功突破了铝塑膜所有的技术封锁。
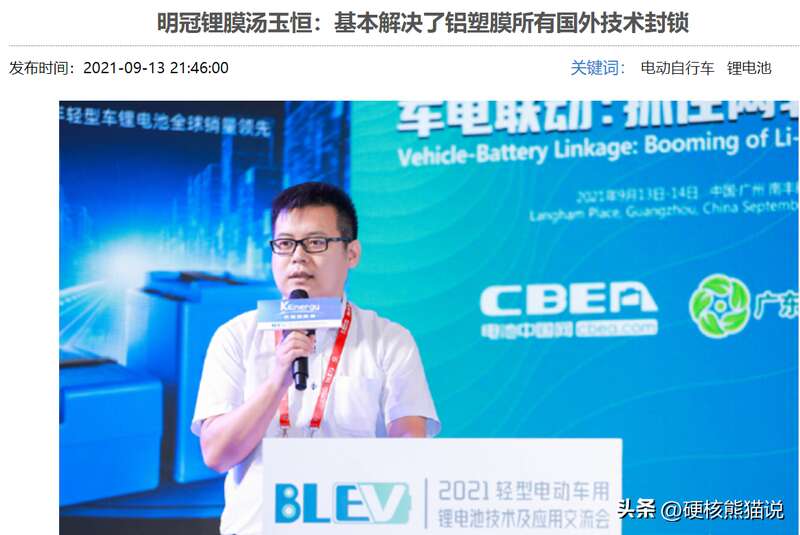
还有新纶科技的技术实力也很强,从2019年开始,他们就与LG合作,向LG提供旗下生产的铝塑膜,2021年,双方再次签署铝塑膜《订购订单》。
我们国产铝塑膜企业的不断突破,正应证了那句话,曾经你看不起我的,如今我用实力征服你!
除了技术外,我们的电池企业也已经今非昔比,全球的动力电池前20名中,有15家是中国企业,他们也都在布局软包电池,并且已经和国产铝塑膜达成了合作协议。
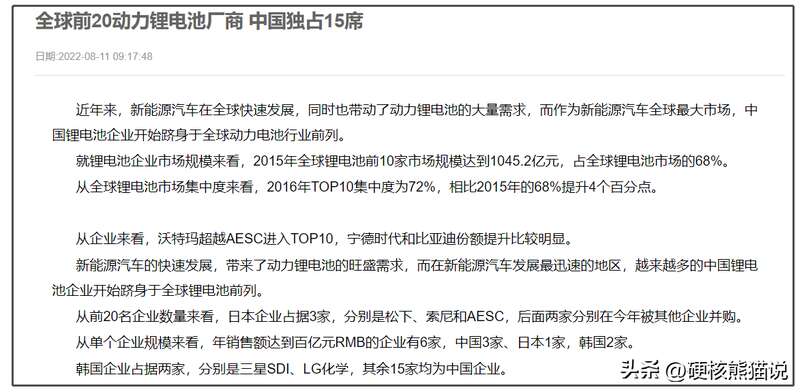
也就是和以前有技术没人用的情况不同,现在我们是兵多将广,粮草充足,于是我们铝塑膜企业的底气也变多了,开始了疯狂的扩充产能模式,有些头部企业在未来3年内,将扩大2-3倍的产能,等这些产能投产后,我国铝塑膜的国产化率将达到60%。
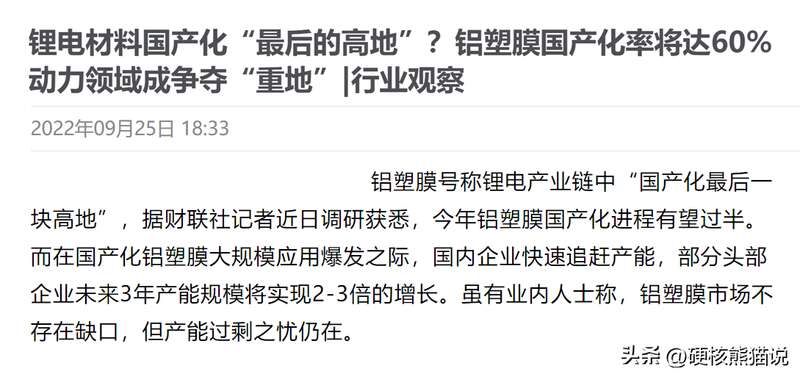
用业内人士说的话说:铝塑膜市场不存在缺口,不用有后顾之忧,只管向电池国产化最后一块阵地发起冲击,将它拿下,而在这之后,我国也将实现锂电池五大材料全部国产化。
到那时,那些曾经对我们不理不睬的企业,也只能抬头仰望我们,熊猫在这边也祝他们早日取得攻坚战的胜利。