本文选自中国工程院院刊《Engineering》2021年第6期,本文来自微信公众号:中国工程院院刊(ID:CAE-Engineering),作者:周龙飞、张霖、方亚隽,原文标题:《随机订单下制造企业的生产触发策略比较丨Engineering》,题图来自:视觉中国
一、引言
传感器技术和物联网的快速发展,使得制造企业可以将资源状态与企业信息系统中的数据同步,更加精确地了解制造资源和制造能力。从宏观的角度来看,云技术使不同制造企业之间的联系更加紧密,协作也更加容易。
目前人们已经建立了一些云制造服务平台,以便以制造服务的形式,整合和共享不同企业的制造资源。借助于这些公共平台,企业能够发布与其制造资源有关的实时信息,并提供客户所需的服务。同时,企业可以通过这些平台收集更加多样化的客户需求。然而,这使得企业更加难以制定生产计划来满足不同的客户。
在由平台、平台管理人、服务提供商和服务需求方构成的制造服务网络中,企业与客户之间的关系为服务提供商与服务需求方之间的关系。只要企业或个人想要寻求合适的服务,以满足其制造需求,那么,他们就可以是平台上的服务需求方。
如果允许将企业的资源或服务公布在平台上并与其他潜在服务需求方共享,那么该企业就可以是服务提供商。平台上的服务管理者通常为管理整个平台上的所有业务的大型公司。
服务管理者通常更关心整个平台的成果和效率,而不是单个公司的生产效率,而单个公司则更关心自己的生产目标。可以采用平均生产时间、平均服务利用率、平均制造成本等统计指标来衡量整个平台的效率。
目前一些研究侧重于协同制造服务网络的全局优化问题,包括服务选择、服务构成和服务调度问题。在研究这些问题时,人们通常考虑优化目标、算法和约束条件。为了组织并优化制造资源,有研究提出了基于分布式遗传算法的资源选择策略。
针对三维(3D)打印服务,有研究者根据3D打印模型的不同属性提出 3D打印服务匹配选择策略,以缩短服务时间。为了通过控制生产来提高多阶段制造系统的能源效率,还有人提出了一种系统性的方法。文献制定了一个数学模型并提出一种物流服务选择方法,用于优化产品从制造商到需求方的交付时间。
此外,还有研究者提出了一种多级聚合服务规划方法,用于处理多粒度的服务,满足服务提供商的需求。就服务构成而言,文献提出了一种资源-服务链组成算法,用于处理时间关系。为了解决最佳服务构成问题,文献提出了一种面向经验知识的遗传算法。
为了处理服务组合问题中不同目标之间的冲突,研究人员对人工蜂群算法进行了改进。就服务调度而言,为了缩短平均任务的交付时间,有研究提出了一种适用于3D打印服务的调度方法。有人提出了一种多任务调度模型,将任务工作量、服务效率和服务数量纳入考虑范围。
此外,有学者还研究了物流服务的调度问题和动态服务调度问题。随着实时传感器和数据同化技术的迅速发展,越来越多的实时数据可用于离散事件的仿真,以实现在线仿真和决策。研究人员基于事件调度仿真方法,制定了适用于汽车总装系统的仿真模型。
动态数据驱动仿真方法很好地解决了实时制造服务的调度问题。以前很少有研究对不同的生产策略进行比较,以期让一家企业能在协同制造环境下进行合适的生产计划,从而满足自己的生产目标。
对于制造企业而言,如何在低库存成本与订单快速交付之间找到一个平衡点,是一个值得研究的问题。一方面,如果企业希望尽快生产并交付产品,就需要提前准备足够的零件和产品,以便可以及时满足随机到达的订单。然而,这些提前准备的零件和产品需要存放数天甚至数月,会不可避免地导致库存成本增加。
另一方面,如果企业希望降低库存成本,那么一种可行的策略是,在接到客户下达的订单之后再开始生产。
然而,该策略可能导致订单交付延迟,从而降低客户满意度。准时生产制(just-in-time, JIT)库存管理和预先生产制(just-in-case, JIC)库存管理是两种典型的库存管理策略。JIT的核心理念是让制造商具备随时可供使用的合适库存,以满足现有需求,同时减少过剩,从而避免额外的库存成本。
JIT策略要求供应商准确地预测需求,以便尽可能多地降低库存成本。相反,使用JIC策略时,制造商要生产足够的零件和产品,并将其纳入库存中,以便在任何时候都能尽可能多地满足客户订单。
因此,JIT旨在降低库存成本,而 JIC策略则旨在加快订单交付速度。在尽可能降低物流成本与材料库存成本总和的情况下,还需确定产品采购量和采购时间的问题。
以前的研究主要侧重于针对不同的生产和库存管理系统开展定性分析或数据统计工作。在本文中,我们提出了不同生产策略的统一理论模型和仿真模型,其中包括时间触发策略、事件触发策略和混合触发策略。
此外,我们还根据这些仿真模型,模拟了不同的生产策略,以便确定生产触发策略对库存成本和订单交付时间的影响。更具体地说,我们提供了生产触发问题的数学模型,并提出了多个生产触发策略(即时间触发策略、事件触发策略和混合触发策略)。
我们针对每一类生产触发策略构建了过程模型,并进行了仿真,以测试其在生产时间和库存成本方面的性能。
X和r分别代表一定时间段内的订单数量以及订单交付率。假设X ~ Pois(r),表明X服从泊松分布。仿真结果表明,当选择合适的时间段(1/r)时,相较于事件触发策略,时间触发策略和混合触发策略的订单交付时间更快、库存成本更低。
本文后续章节内容如下:第2节将分析企业的主要生产过程,并给出其数学描述;第3节将提出三类不同的生产触发策略,并构建其仿真模型;第4节将进行仿真实验,以比较不同生产触发策略的性能;第5节将给出结论并探讨下一步的工作。
二、问题描述
1. 制造服务网络
可以通过复杂的制造供需网络,描述协同制造环境中服务提供商与服务需求方之间的关系。企业通常充当服务提供商的角色,并根据其制造资源和制造能力,提供多种类型的制造服务。我们可以使用服务粒度模型,对制造服务进行描述,以代表不同的制造服务级别。
最简单的服务被称为单元服务,这些服务都是由单一的制造机器或制造工具提供的。可以将多单元服务组合从而发挥更加复杂的制造功能的服务。
在本文中,我们考虑了一个级别更高的制造服务模型,在该模型中,企业被封装为单一服务,其输入和输出分别为客户订单和成品。本文旨在研究随机输入情况下企业内部不同生产策略对输出表现的影响。
一方面,由于制造服务的灵活性,其通常可以执行多种类型的子任务。例如,一家企业可能会提供一个计算机数控(CNC)机床加工服务,这是一项十分典型的制造服务。计算机数控机床加工服务可能会为多项机床加工任务提供支持,如柱、锥、球、螺纹、平面、槽、齿轮和孔等任务。
另一方面,由于不同的企业可能会争相去提供同一类服务,因此,不同的制造服务可以执行特定类型的子任务。根据上述分析,制造服务与子任务之间的映射关系为多对多的关系。
此外还存在其他的不确定性,如随机订单以及随机服务故障。通常,单位时间内下达的订单的数量基本服从泊松分布,即Pois(r),式中,r为订单到达率。订单到达制造平台时,根据订单类型,将其匹配给平台上的某类制造服务。
图1展示了一个具有两个服务需求方和两个服务提供商的协同制造服务网络。可以看出,需求方D1向制造平台提交了一个订单O1,平台将该任务分配给提供商 P2。基于这一匹配,构建出提供商P2与需求方D1之间的供需关系。
执行完成订单O1的生产后,提供商P2向需求方D1交付订单O1所需的产品。此外,需求方D2向平台提交订单O2,平台将订单O2分配给供应商P1。
同样通过制造平台,构建出提供商P1与需求方D2之间的供需关系。执行完成订单O2的生产后,提供商P1向需求方D2 交付订单O2所需的产品。
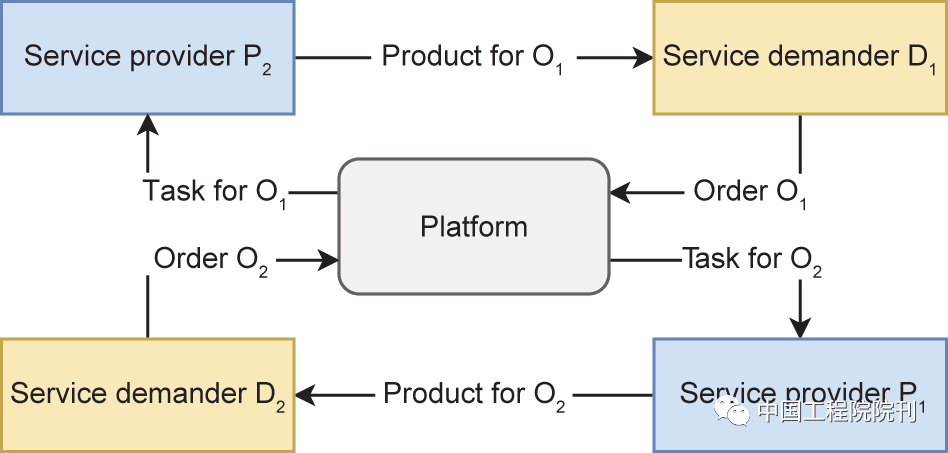
2. 生产过程
生产过程可以简单地划分为多个主要阶段,其中包括材料输入、零件生产、零件存放、产品组装和产品存放。对于企业而言,可以将客户下达的订单视为制造系统的信息输入,而材料则可以被视为实际投入。
材料来自供应链上的上游供应商,而订单则来自供应链上的下游客户。产品是企业制造系统的输出。企业在执行完成生产过程(包括零件生产和产品组装)后,将产品存放在产品库存中,最终将产品交付给客户。
图2简要介绍了一家电子组件制造企业的生产过程 “包括从原料(左侧)到产品(右侧)”。对于不同类型的材料,设立不同的材料库。在电子组件制造行业,材料主要包括印刷电路板和电子元件。
当制造系统开始生产时,材料被自动送往零件生产线上。在零件生产线上,材料经过加工,形成不同类型的零件。特别是对于电子组装行业而言,通过表面贴装技术线,将电子元件安装在印刷电路板上,从而制造出不同类型的零件。
然后将制成的零件送往零件库中存储起来,供将来使用。产品组装线从零件库存中取出一定数量的零件,将其组装成产品。组装完成后将产品存放在产品库存中。最后,通过物流将产品交付给客户,完成订单。
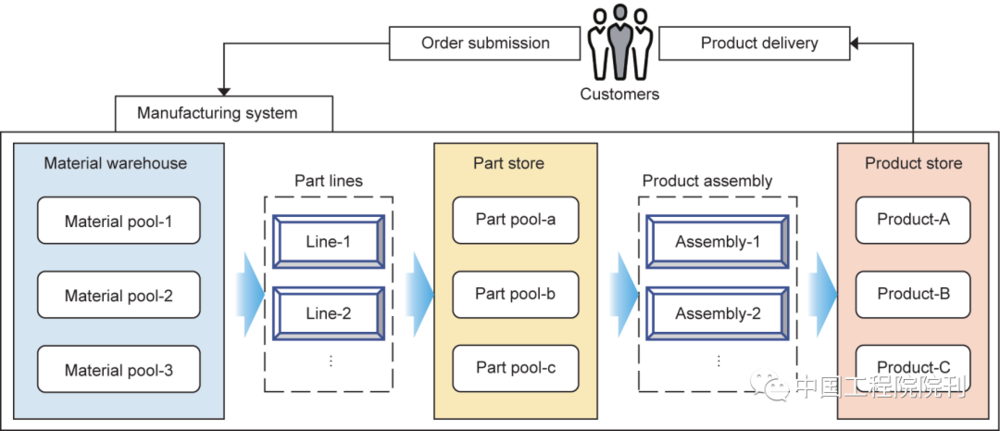
3. 数学描述
鉴于动态环境下订单随机到达,因此需要选择某一时间段进行分析。ts和te分别代表研究持续时间段内的起始时间和结束时间。
Oi代表在时间Ai抵达的第i个订单。订单Oi 到达后,由触发策略触发制造系统,制造系统立即开始执行订单Oi的生产过程。制造系统完成整个生产过程(包括零件生产和产品组装)后,生产出Oi的产品。
优化目标
在本研究中,我们主要考虑了这一问题的两个优化目标:订单交付时间和库存占用率。Ci代表订单Oi的完成时间,可以由式(1)得出订单交付时间的优化目标。

式中,N为时间(ts, te)期间到达制造系统的所有订单的数量,由式(2)确定。

因此,订单交付时间的优化目标还可以表示为式(3)。

库存占用率优化目标包括零件库存和产品库存。Ipart(t)和Iprod(t)分别代表时间t 时的零件库存占用率和产品库存占用率。用ts与te之间的库存占用总量除以(te− ts),得到平均库存占用率。
式(4)和式(5)分别代表平均零件库存占用率和平均产品库存占用率的表达式。
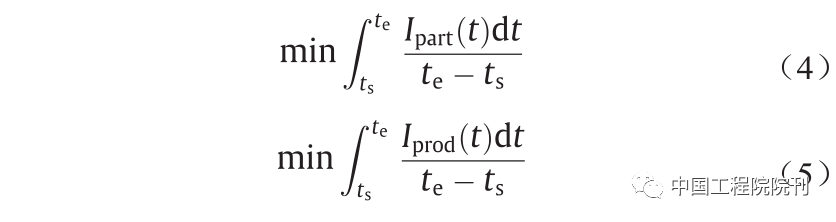
在实际应用中,订单交付时间和库存成本是相互矛盾的。我们需要调合它们,并找到一个适宜的平衡点。
订单到达时间分布
在所有仿真模型中,每个时间段内到达的订单数量 X均服从相同的泊松分布Pois(r)。因此,X~Pois(r),如式(6)所示。

式中,r为模型中的订单到达率,它实际上为每个时间段的平均订单数。Bi 代表Oi到达与Oi−1到达之间的间隔时间,可以由式(7)得出。

式中,A0 = 0,并且i≥1。在仿真模型中,Bi 服从相同的指数分布Exp(r),定义为Bi~ Exp(r)。由式(8)得出Bi 的累积分布函数。

图3显示了到达时间函数模块的详细结构。到达时间函数的输入和输出分别为到达率和到达时间。每次订单到达均会触发到达时间函数,然后模型得到该订单的到达时间。我们将多个仿真模型中的到达率r设定为0.5。在进行仿真时,我们将根据到达时间函数,随机生成客户订单。
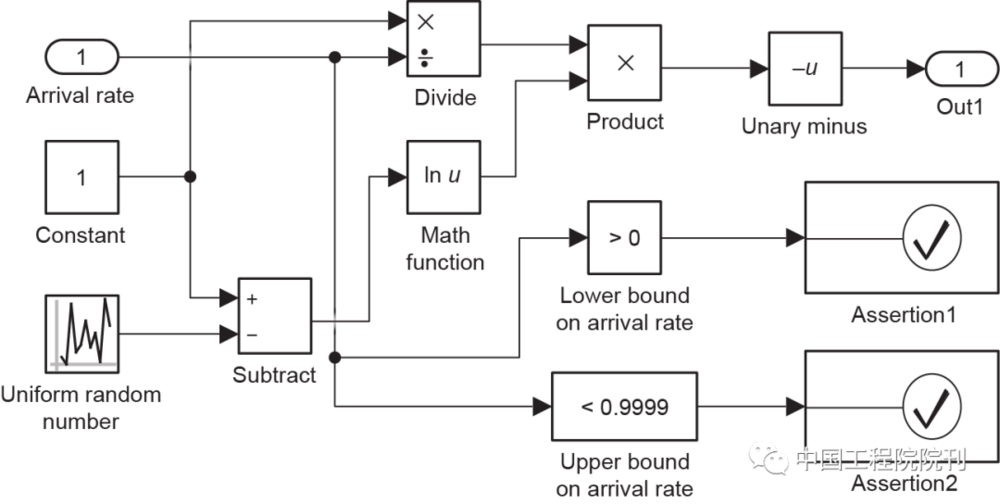
三、生产触发策略
在制造服务网络中,服务提供商需要根据订单到达和服务可用性等系统状态,动态调整其生产策略。对于制造企业而言,生产触发策略是最重要的生产策略之一。
本节将介绍三类生产触发策略:时间触发策略、事件触发策略和混合触发策略。Tpart(i)代表第i个零件的触发时间,Tprod(j)代表第j个产品的触发时间。因此,可由 Tpart(i)和Tprod(j)完全决定生产触发策略。
1. 时间触发策略
在批量生产模式下,企业通常会根据生产计划,定期生产大批零件和产品。批量生产模式属于一种时间触发生产策略。在时间触发生产策略中,按照特定的时间周期性地触发零件生产过程和产品组装过程。
在时间触发模型中,企业根据特定的时间段进行生产,而不会考虑订单到达情况。τpart和τprod分别代表零件生产触发时间以及产品组装触发时间。
由零件触发时间Tpart(i)和产品触发时间Tprod(i)表示时间触发策略,如式(9)和式(10)所示。
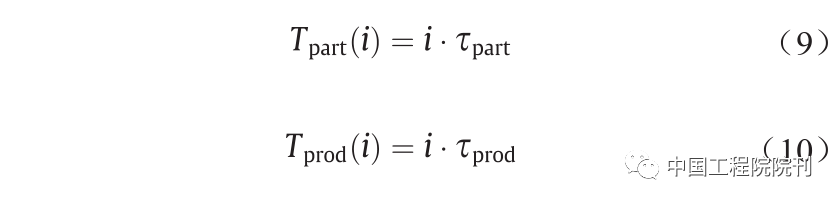
图4为时间触发生产策略模型。图左侧的开头有一个零件触发条件,该零件触发条件触发零件生产线执行零件的生产过程。零件生产线生产完零件后,将其运往零件库存。
在零件库存之后的是产品组装线,产品组装线在每个时间段结束后执行产品组装过程。产品组装线装配好产品后,将产品存放在产品库存。一旦有与订单匹配的产品,产品库存就会将匹配的产品交付给订单客户。产品交付部分执行订单匹配过程和产品交付过程。
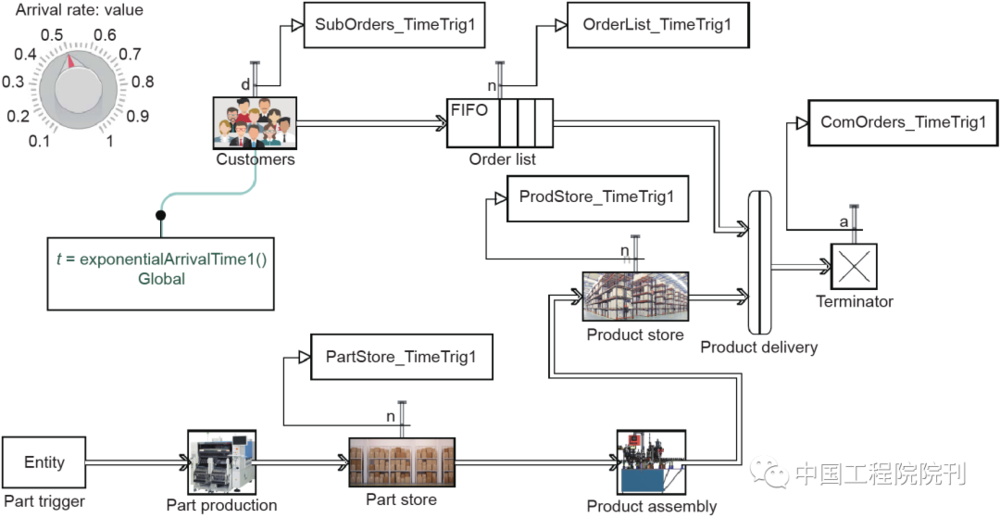
可以看出,在时间触发生产模型中,零件生产和产品组装都是由一定的时间段触发的,并且与订单情况无关。在每个时间段内,零件生产线生产出一定数量的不同类型的零件。这些零件将被立即存放到零件库存。
产品组装线同样在每个时间段内生产出一定数量的产品,这些成品随后被立即存放到产品库存。
注意,即使在同一家企业,零件生产和产品组装的时间段通常也是不同的。这两个时间段往往与特定的行业、产品类型和生产节拍有关。在该模型中,当收到订单时,企业将产品库存中的产品交付给客户。如果没有足够的产品满足订单,企业将会等到生产出足够的产品时才交付。
因此,生产过程不会受到订单的影响。即使库存中存放了足够的产品,生产过程仍然按照一定的时间段继续进行,生产过程也不会提速。
2. 事件触发策略
在个性化定制生产模式中,企业通常根据事件触发策略来制定其生产计划,即产品规模和产品类型是依据客户的订单所确定的。在时间触发生产模式中,零件生产过程由订单到达触发。Tpart(i)代表零件触发时间,如式(11)所示。

只有当至少一条产品组装线可用且零件库存中没有先于Oi 的其他零件时,才能触发Oi 的产品组装过程。Spart(i)和Sprod(i)分别代表Oi 的零件生产时间和产品组装时间。
当i = 1时,O1的产品组装触发时间为O1的到达时间加上零件生产时间Spart(1),如式(12)所示。

当i ≥2时,由递归函数确定Oi 的产品组装触发时间 Tprod(i),如式(13)、(14)、(15)所示。

式中:


事件触发生产策略模型见图5。不同于时间触发生产策略,在事件触发生产策略模型中,零件生产活动和产品组装活动均由特定的事件触发。特别是当订单到达时,将根据订单的类型和数量,为零件生产和产品组装工作制定生产计划。
零件生产线开始根据生产计划,生产相应的零件。零件生产线生产完零件后,将其运往零件库存。
在零件库存之后的是产品组装线,产品组装线执行产品组装过程。产品组装线装配好产品后,将产品存放在产品库存中。
一旦产品库存中有与订单匹配的产品,就会将该匹配的产品交付给订单客户。产品交付部分执行订单匹配过程和产品交付过程。在事件触发生产模型中,库存总是用于临时存放零件和产品。一旦产品组装线收到零件,则开始组装。一旦产品进入产品库存,就会通过物流把产品交付给客户。
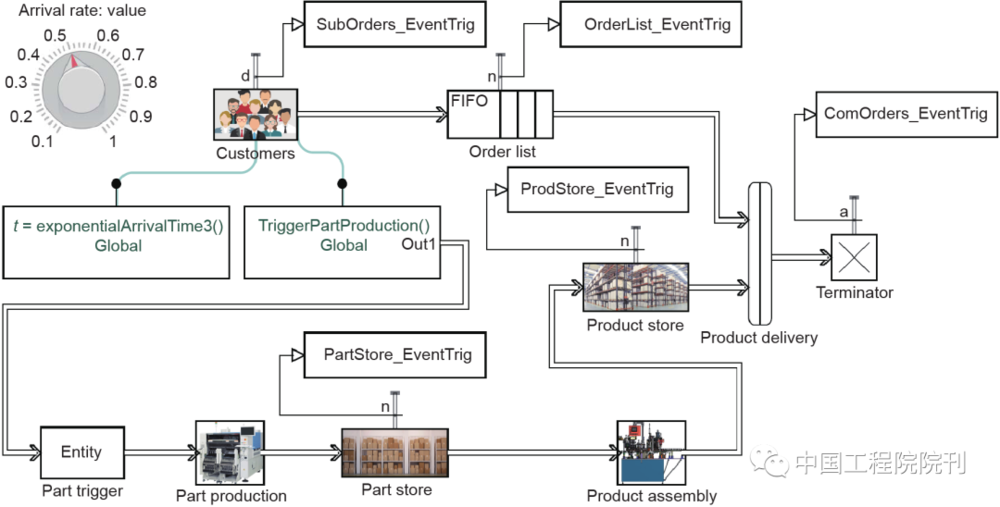
3. 混合触发策略
混合触发策略的生产模型见图6。不同于时间触发生产策略和事件触发生产策略,在混合触发生产模型中,零件生产过程由时间触发,而产品组装过程则由事件触发。
在该模型中,零件生产线在各时间段内生产出一定数量的零件。零件生产时间段由Tpart(i)代表,如式(16)所示。


在混合触发模型中,订单量不会影响零件生产过程,但会影响产品组装过程。混合触发模型中的产品库存用于临时存放产品,这是因为产品一旦制造完成,库存中的所有产品都会被立即交付给客户。
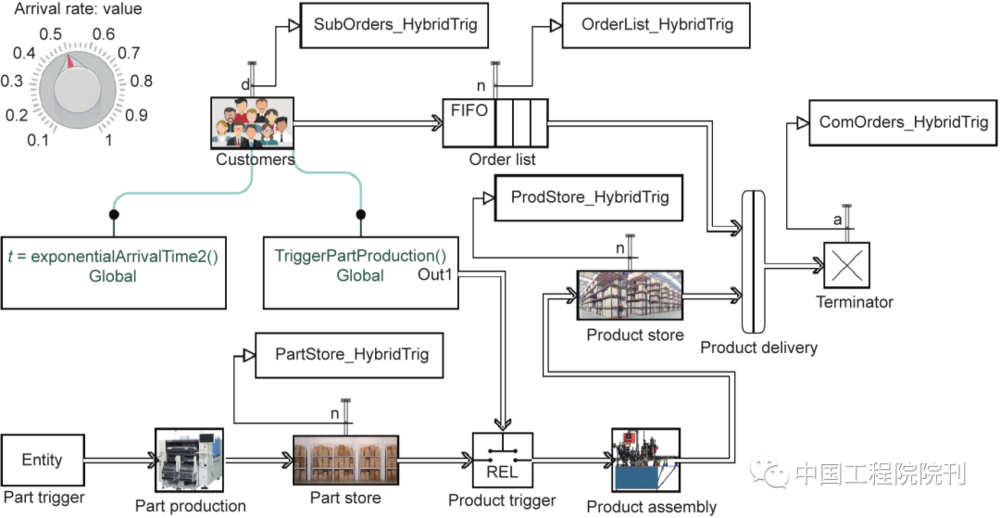
四、仿真
为了测试这些拟定的策略的性能,我们设计了不同的仿真实验,并研究产品触发策略在订单随机到达的情况下对生产性能的影响。我们为不同的触发策略建立了仿真模型,然后通过SimEvents进行多次仿真。
1. 案例背景
在本案例研究中,选择5家企业作为制造服务网络中的服务提供商。我们为这5家企业构建了5个模型来进行仿真。每个模型的仿真时间设置为1000个时间段。
将部分基本模块(如零件触发条件、零件生产、零件储存、产品组装、产品储存、客户、订单列表和产品交付)纳入每个仿真模型。表1列出了所有仿真模型的订单到达率、零件触发条件和产品触发条件。
表1 仿真模型参数设置
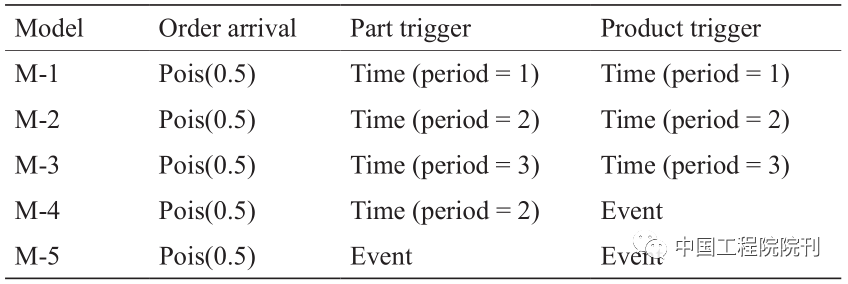
结果表明,模型-1、模型-2和模型-3由时间触发。尽管如此,模型-1、模型-2和模型-3的时间段各不相同,可将这一点用于研究时间段对生产性能的影响。模型-4 为混合触发模型:零件生产线由时间触发,周期为2,而产品组装线则由到达订单触发。
模型-5由事件触发,因此,零件生产线和产品组装线均由到达订单触发。这些仿真模型有两种触发条件,即零件触发条件和产品触发条件。零件触发条件适用于事件触发模型(模型-5),产品触发条件适用于混合触发模型(模型-4)。
5个生产模型的产品库存能力均设定为100,零件库存能力均设定为“inf”(即无限大)。仿真过程的到达订单数量如图 7所示。
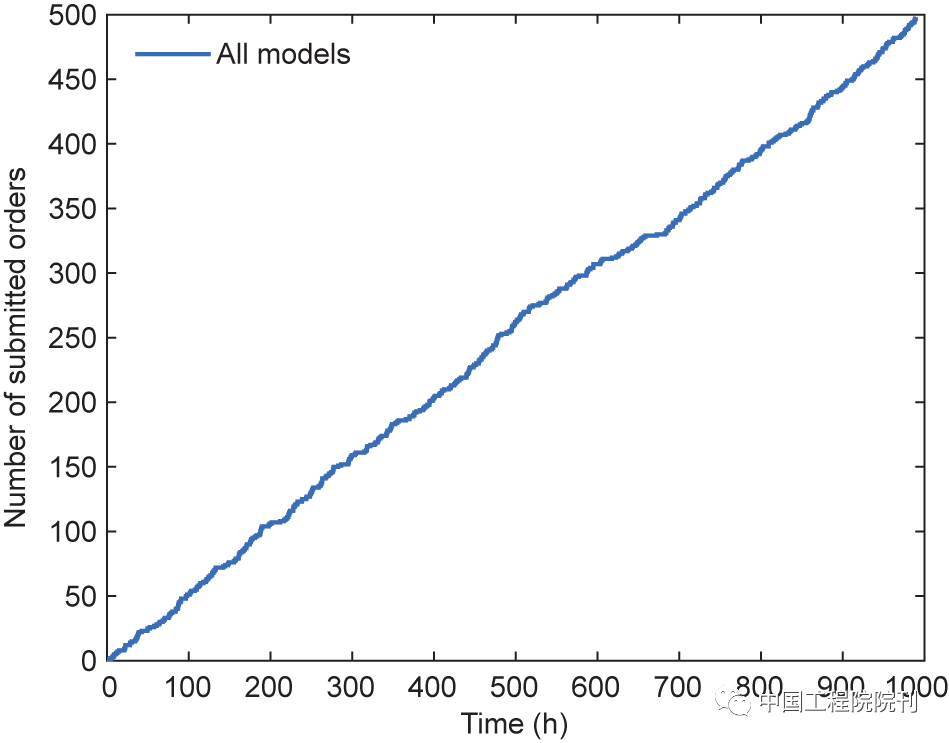
2. 结果
仿真期间,为了比较不同策略之间的任务交付和库存成本,我们统计了每个生产模型的几种数据。在任务交付方面,我们比较了这5个生产模型的两个指标:等待订单数量和已完成订单数量。在库存成本方面,我们针对这5个生产模型,比较了库存零件数量以及库存产品数量。
因此,我们从4个方面比较了不同的生产触发策略:等待订单数量、已完成订单数量、库存零件数量以及库存产品数量。下文给出了这些评价指标的定义。
等待订单数量指的是订单列表上的订单数量,如图 4至图6所示。等待订单数量实际上为输入订单数量(即客户提交的到达订单的数量)减去已完成订单数量(即已完成产品数量)。
已完成订单数量指的是已完成并交付给客户的所有订单的数量。该值实际上等于图4至图6中到达终端的订单数量。只有当成品与订单匹配后,才认为完成了该订单。
库存零件数量指的是当时零件库存中的零件数量,如图4至图6所示。库存零件数量等于零件生产线生产的零件数量减去用于组装产品的零件数量。
库存产品数量指的是当时产品库存中的产品数量,如图4至图6所示。库存产品数量等于由产品生产线组装的产品数量减去根据订单交付给客户的产品数量。
图8比较了5个生产触发模型的等待订单数量随时间变化的结果。如图8所示,仿真期间,时间触发模型(周期= 1,周期= 2)和混合触发模型的等待订单数量变化幅度远远小于时间触发(周期=3)模型和事件触发模型。
到仿真时间(te = 1000 h)结束时,时间触发(周期=3)模型和事件触发模型的等待订单数量分别达到170和90。这一结果表明,时间触发(周期=1、周期 =2)模型和混合触发模型在等待时间结束时,等待订单数量会收敛,而时间触发(周期=3)模型和事件触发模型的等待订单数量则不会收敛。
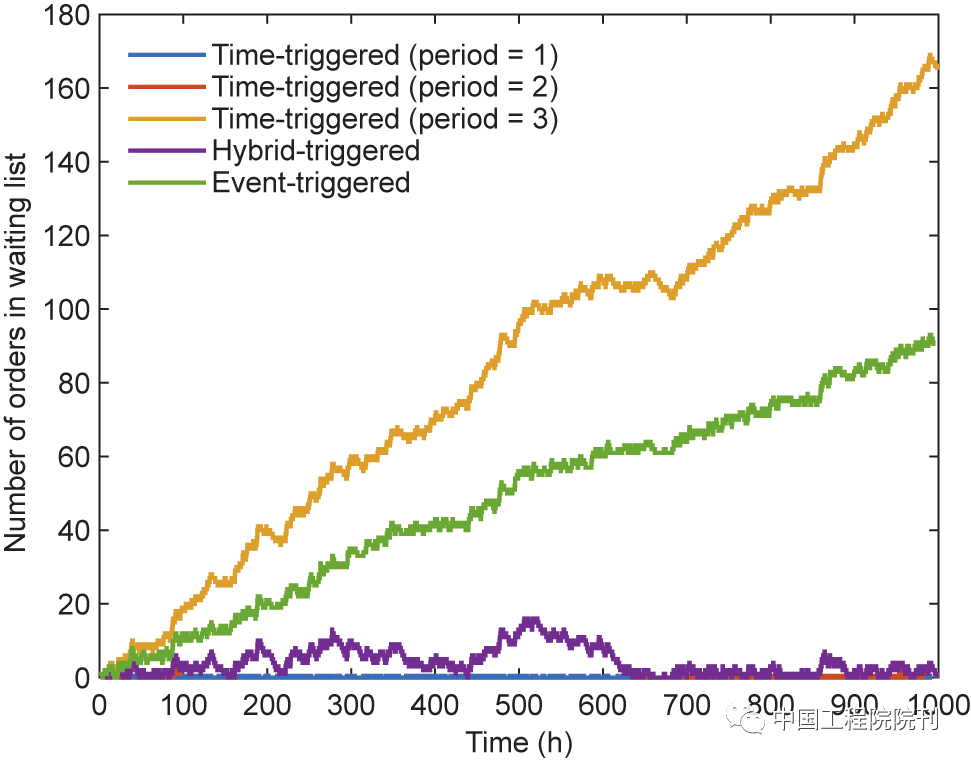
图9比较了5种生产触发模型的已完成订单数量随时间变化的结果。如图所示,在从起始时间(ts = 0 h)到结束时间(te = 1000 h)的整个仿真过程中,5个生产模型的已完成订单数量均持续增加。就已完成订单数量而言,周期更短的时间触发模型(即周期=1和周期=2)以及混合触发模型在整个过程中的性能几乎相同。
有时(t = 500 h和t = 600 h之间),周期更短的时间触发模型(周期=1)的性能要略微优于时间触发模型(周期=2)和混合触发模型。就已完成订单数量而言,周期更长的时间触发模型(周期=3)以及事件触发模型的性能要逊于周期更短的时间触发模型(周期=1、周期=2)和混合触发模型。
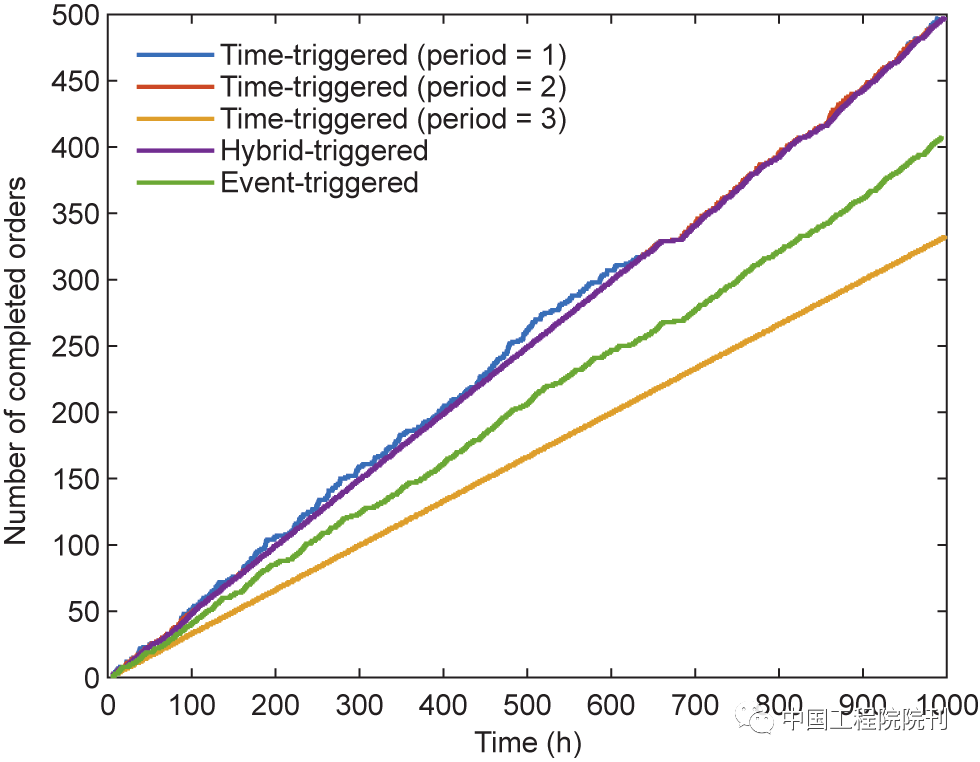
图10比较了5个生产触发模式的库存零件数量随时间变化的结果。如图所示,在从起始时间(ts = 0 h)到时间600(t = 600 h)这段时间内,5个模型的库存订单数量总是接近于零。从时间600(t = 600 h)到结束时间(te = 1000 h),时间触发(周期=2、周期=3)模型和事件触发模型的零件库存仍然接近于零。
然而,t = 600 h之后,混合触发模型的库存零件数量出现波动。此外,t = 600 h之后,时间触发(周期=1)模型的库存零件数量迅速增加。因此,就库存零件性能而言,时间触发(周期=2、周期=3)模型和事件触发模型的表现十分优异,而混合触发模型的表现虽然并不理想,但也合理;然而,时间触发(周期=1)模型的性能很差。
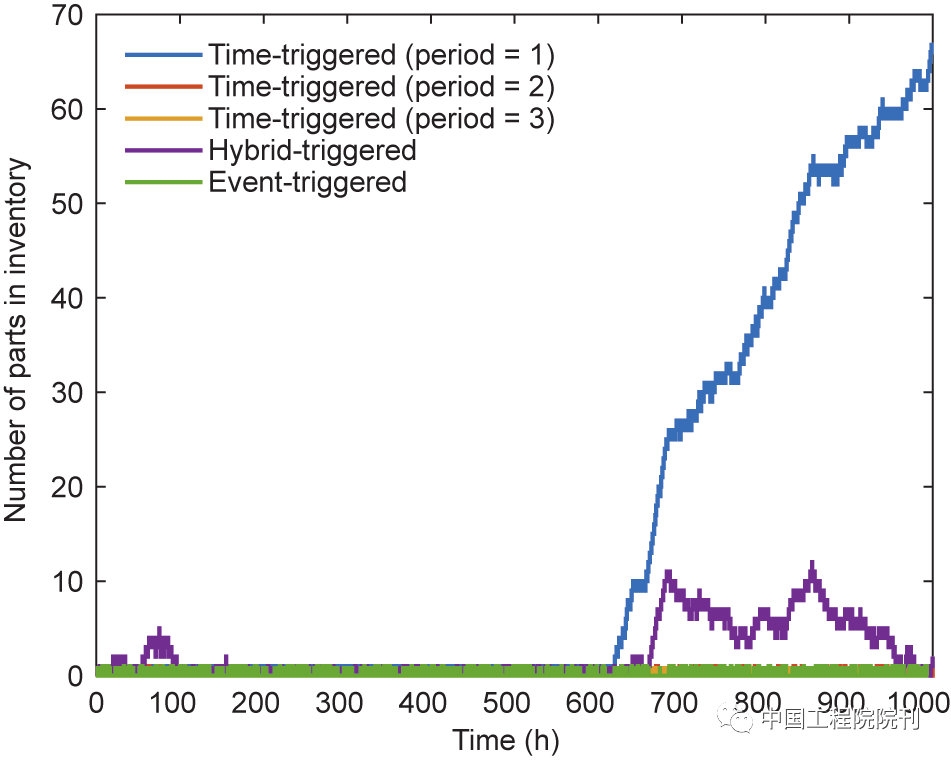
图11比较了5个生产触发模型的库存产品数量随时间变化的结果。如图所示,时间触发(周期=2、周期 =3)模型、混合触发模型、事件触发模型的性能很好,但在t = 650 h到t = 950 h的这段时间内,时间触发(周期=2)模型出现小幅波动。
相较于其他4个模型,时间触发(周期=1)模型在产品库存方面的性能较差。时间 t = 600 h时,时间触发模型(周期=1)的库存产品数量达到最大库存容量,即100(参见第4.1节)。
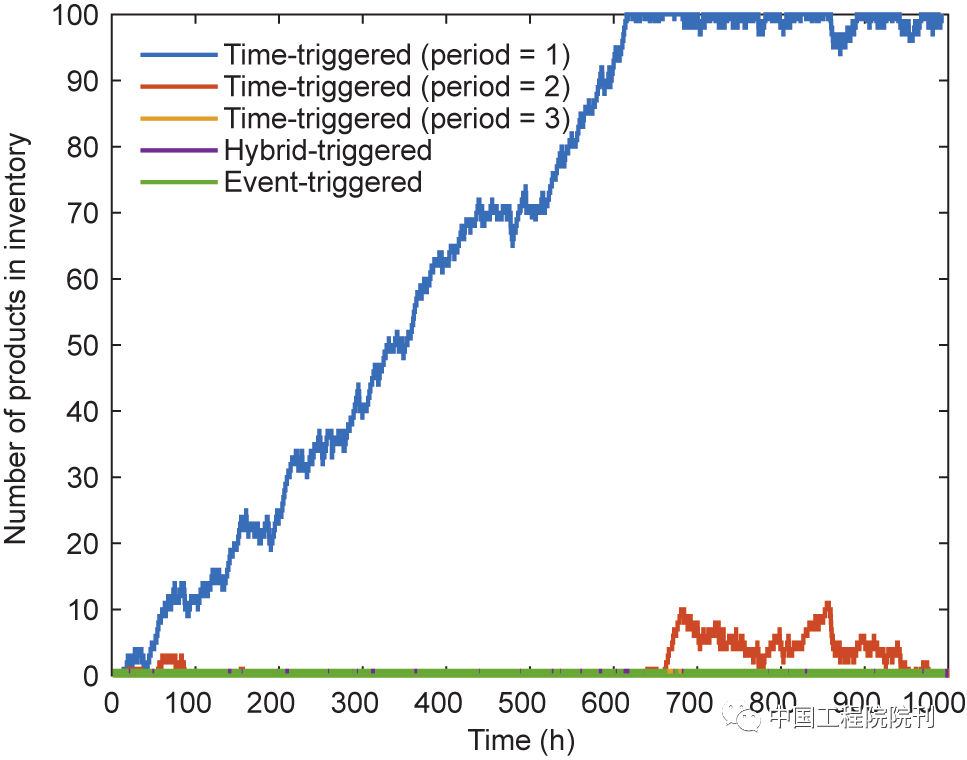
3. 讨论
仿真结果表明,生产周期是时间触发生产策略的一个关键因素。在该策略中,企业在制定生产计划时,不考虑订单到达情况。本研究将仿真模型的订单到达率r 设定为0.5。因此,单位时间订单到达数量的预期值为 1/r = 2。
如仿真结果所示,将时间触发策略的周期τpart和 τprod设置为2时(如模型-2),模型在订单交付时间和库存占用率方面的性能较好。当τpart = 1且 τprod= 1时(如模型-1),时间触发模型在订单交付时间方面的性能较好,但零件库存占用率和产品库存占用率要高于其他策略,如图10和图11所示。
当τpart=3且τprod=3时(如模型-3),时间触发模型在库存占用率方面的性能较好,但同期交付订单数量则比其他策略少得多,如图8和图9所示,这表明该模型的订单交付时间要超过平均时间。
如图10和图11所示,事件触发生产策略的库存占用率最低,这导致库存成本最少。然而,事件触发策略的订单交付时间要长于时间触发策略(周期=1、周期=2)以及混合触发策略,但如图8和图9所示,它仍然略优于时间触发策略(周期=3)。
混合触发策略有令人满意的订单交付时间。虽然存在一些局部性的波动,但该策略的总体性能优异。此外,混合触发策略在零件库存占用率和产品库存占用率方面的性能较好。尤其是在产品库存方面,混合触发策略的性能最好,如图11所示。
因此,如要在订单交付时间与库存成本之间找到一个平衡点,混合触发生产策略就是一个明智的选择。
总的来说,如果订单到达时间呈泊松分布Pois(r),那么,制造服务网络中的制造企业就应该选择混合触发策略或者周期τ = 1/r 的时间触发策略,这是因为这两个生产策略在订单交付时间和库存成本方面的性能较好。使用这两种策略中的任意一种策略都能在订单交付时间与生产成本之间找到一个平衡点。
周期τ > 1/r的时间触发策略以及事件触发策略均能提供较低的库存成本,但它们的订单交付时间较长,导致客户满意度降低。周期 τ < 1/r 的时间触发策略在缩短订单交付时间方面性能较好,但它在生产过程中会占用大量的库存。
五、结论
针对动态协同制造环境下的生产触发问题,我们提出了制造企业在订单随机到达情况下的三种生产触发策略:时间触发策略、事件触发策略和混合触发策略。我们构建并模拟了这三种生产触发策略的仿真模型,以便研究它们在订单交付时间和库存成本方面的性能。此外,我们还改变了时间触发策略和混合触发策略的周期,以便研究周期对系统性能的影响。
仿真结果表明:
①混合触发策略和周期τ = 1/r 的时间触发策略在订单交付时间和库存成本方面的性能要优于其他策略;
②周期 τ > 1/r 的时间触发策略以及事件触发策略的库存成本较低,但订单交付时间较长;
③周期τ < 1/r 的时间触发策略在订单交付时间方面性能较好,但在库存成本方面性能较差。
未来的研究方向是根据生产过程以及零件类型与产品类型之间的关系,设计出更加详细的生产模型。另一个方向则是研究更为复杂的制造服务网络,如云制造、社会化制造环境。
改编原文:
Longfei Zhou, Lin Zhang, Yajun Fang.Comparison of Production-Triggering Strategies for Manufacturing Enterprises under Random Orders[J].Engineering,2021,7(6):798-806.
本文来自微信公众号:中国工程院院刊(ID:CAE-Engineering),作者:周龙飞、张霖、方亚隽,本文较原文略有调整,来源:Comparison of Production-Triggering Strategies for Manufacturing Enterprises under Random Orders[J].Engineering,2021,7(6):798-806