本文来自微信公众号:中国工程院院刊(ID:CAE-Engineering),作者:栾恩杰、王崑声、胡良元、赵滟、毛寅轩、陈红涛、崔剑,本文选自中国工程院院刊《中国工程科学》2016年第4期,原文标题:《提升我国航天装备制造能力的思考丨中国工程科学》,题图来自:视觉中国
2021年6月17日9时22分,搭载神舟十二号载人飞船的长征二号F遥十二运载火箭,在酒泉卫星发射中心点火发射。此后,神舟十二号载人飞船与火箭成功分离,进入预定轨道,发射取得圆满成功,这是我国空间站阶段的首次载人发射任务。航天装备是国家空间基础设施建设和卫星应用产业发展的使能资产,航天装备制造是先进制造业的典型领域。航天装备制造能力决定了国家进入太空、控制太空和利用太空的能力,是国家卫星及应用产业的基础与核心。航天装备制造产业是国家战略性新兴产业,是建设航天强国和制造强国的重要支撑。
中国工程院栾恩杰院士科研团队在中国工程院院刊《中国工程科学》撰文,从航天装备及其制造过程的特点分析了我国航天装备制造系统能力的构成,并结合我国航天装备制造的发展趋势,分析了我国航天装备制造存在的突出问题,提出了提升我国航天装备制造能力的对策建议。文章指出,要针对我国航天装备制造存在的短板和瓶颈问题,通过构建先进的航天制造模式,强化工艺创新,突破航天制造装备技术瓶颈,强化人才队伍建设和营造有利的发展环境等举措,实现我国航天装备制造能力跨越式发展,推动我国航天强国的建设。
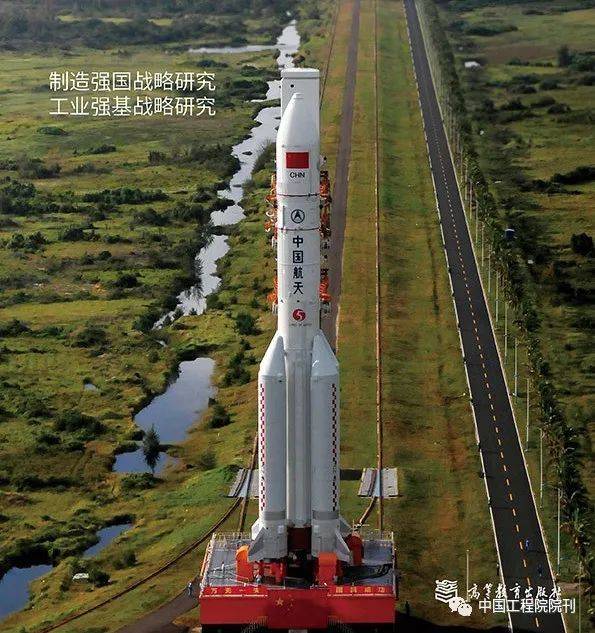
一、前言
经过多年的发展,我国已形成自主完善的航天科技工业体系,具备了较强的航天型号研制能力和航天装备制造能力,圆满完成了以载人航天、月球探测等为代表的国家重大航天任务,圆满完成了各类各型运载火箭、应用卫星及战略、战术导弹武器的研制和生产任务,有力推动了我国航天科技进步和经济社会发展,为增强国家的综合国力、国防实力与民族凝聚力作出了贡献。
航天装备是国家空间基础设施建设和卫星应用产业发展的使能资产,航天装备制造是先进制造业的典型领域。航天装备制造能力决定了国家进入太空、控制太空和利用太空的能力,是国家卫星及应用产业的基础与核心。航天装备制造产业是国家战略性新兴产业,是建设航天强国和制造强国的重要支撑。世界航天大国无不将新型运载火箭、大容量通信卫星、高分辨率遥感卫星和全球导航卫星等航天装备作为重点投入领域。世界航天的发展历程表明:航天装备的发展水平决定了航天发展的高度,航天装备体现了国家意志,没有自主可控的航天装备制造能力,就没有坚实、可持续发展的航天能力和航天产业。
习近平总书记指出,发展航天事业,建设航天强国,是我们不懈追求的航天梦。当前,世界经济发展环境发生了复杂而深刻的变化,制造业面临严峻的发展形势。加快结构调整,推进产业升级,推动我国由制造大国向制造强国转变、由航天大国向航天强国转变的战略任务,对我国航天装备制造的能力和技术水平提出了更高要求,亟需以我国航天装备制造的现实需求为牵引,大力提升我国航天装备制造能力,推动航天强国建设。
二、航天装备制造的内涵与特点
(一)航天装备的特点
航天装备制造特指运载火箭及空间运载器、卫星、飞船、空间站、深空探测器、导弹武器以及相关地面保障设备等产品的制造。
航天装备作为主要在地面建造但在空间环境中运行的一类特殊产品,具有如下特点:
战略地位重要。作为航天产业发展的物质基础、执行国家航天任务的载体和提升国家制天权能力的重要领域,航天装备制造具有重大的战略意义,难以从国外引进,必须坚持走自主可控的发展道路。
技术构成复杂。航天装备高度复杂,由多学科、多领域的技术所集成,是技术高度密集的复杂工程系统。航天装备制造具有极强的探索性、定制性,是一个逐步吃透设计意图、持续提升工艺成熟度的过程。
使用环境严酷。航天装备在空间环境中工作,面临真空、微重力、极端温度、原子氧、高能带电粒子、空间碎片等因素的考验。因此,航天装备制造必须要充分考虑严酷的空间环境所造成的影响,采取有效的防护技术和措施。
保障服务困难。目前,除空间站外,所有在轨航天装备均无人值守,出于技术可行性和经济可承受性的考虑,很难对在轨航天装备开展保障服务。因此,航天装备必须要具备极高的可靠性,这种可靠性可通过设计、工艺、生产、试验等过程来实现,对航天装备制造提出了更高的挑战。
单件价值极高。航天产品性能和性质特殊,完成特定任务和功能无需较大批量,与其他装备制造业相比,不具有较强的规模效益,但是单件产品的价值极高,具有量少而附加值高的特点。
安全防护严格。目前,航天装备产品中含有有毒有害物质,如常规液体火箭的推进剂硝基氧化剂和各种肼类燃料,这些物质具有强氧化性、腐蚀性、毒性和易燃易爆特性,制造过程中需要采取严格的防护措施,这对航天装备制造过程的安全性提出了极高要求。
(二)航天装备制造过程的特点
航天装备制造系统是指以生产航天装备产品为目的,由制造过程中的人员、物料、能源、软硬件设备以及相关设计方法、加工工艺、生产调度、系统维护、管理规范等组成的具有特定功能的有机整体,航天装备制造系统是航天工业体系的重要组成部分。
航天装备制造系统受人员、机器设备设施、物料、环境等多种因素的影响和制约。同时,航天装备本身复杂的技术构成、严酷的使用环境和困难的保障服务等特点,都大大提升了航天装备制造过程的复杂程度和困难程度,主要表现为:
1. 航天装备体系结构复杂、分系统之间交互耦合
航天装备设计难度大,技术状态变换频繁,产品数据信息繁多;航天装备制造工艺复杂,涵盖材料选用、工序安排、刀具使用、装夹方式、切削参数、装配方法、质量检验等内容;航天装备制造现场环境复杂,涉及设备布局、产品流转、资源调度等方面。
2. 航天装备呈现多型号并举、研制与批产并重的局面
航天装备既需要实现面向用户需求的多品种个性化定制,也需要基于平台化、模块化、产品化等手段保证批产任务的完成,存在着广泛的“多品种、小批量”的生产需求。
3. 质量可靠性要求高,计划进度要求紧,任务计划多变,要求“一次成功”
航天装备装配过程复杂,难以实现自动化流水线式的批量生产,对航天装备组织生产的柔性提出了极高的要求。
为了有效应对航天装备制造过程的复杂性,我国航天制造业在组织管理、系统工程、质量管理等方面形成了一套行之有效的方法。
一是严密的组织管理过程。航天装备制造是典型的跨学科、跨部门、跨地域的复杂制造过程,涉及设计、生产、试验、采购、物流、测试等多个环节,形成了以总装集成单位为龙头,由各分系统、单机、部件单位和外协配套单位组成的复杂生产协作网络;建立了以总指挥、总设计师、总工艺师为核心的责任主体,以产品分解结构、实物配套表为依据,以各级齐套单位为关键节点,以配套链条为纽带,以科研生产计划为标尺的一套自上而下、逐层分解、严密有序的组织管理体系。
二是严格的系统工程过程。航天装备高度的技术复杂性决定了航天装备的制造必须严格遵守总体→分解→集成的系统工程过程,必须严格按照方案、初样、试样、定型等不同阶段的研制程序,坚持设计决定制造可行性、制造验证设计合理性的系统理念,特别注重装配、验证和试验等环节,持续提升航天装备制造技术成熟度和制造成熟度。
三是严苛的质量管理要求。航天装备产品质量具有特殊的政治影响和社会影响,需要满足高质量、高可靠性的需求,以及小子样、一次成功的特殊要求。我国航天装备制造坚持“系统质量观”,培育了“严慎细实”和“零缺陷”的质量理念,建立了型号研制单位抓质量体系运行,型号项目团队抓质量保证大纲实施的矩阵式产品保证体系,形成了技术、管理归零“双五条”标准等一系列相关配套标准规范。
(三)航天装备制造系统能力的构成
装备制造能力是装备制造系统效能的直接反映。航天装备制造系统能力包括技术能力和管理能力两个方面,如图1所示。
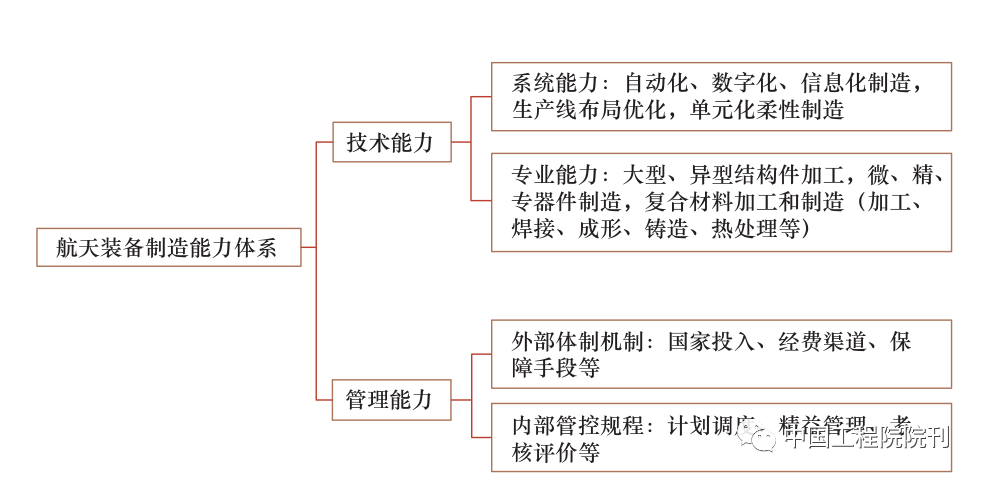
技术能力包含系统能力和专业能力。系统能力反映了航天装备制造系统在总体层面所表现出来的技术水平和效益、效率,是企业制造模式的直接体现,包括制造系统的数字化和自动化水平,如计算机辅助设计(CAD)、计算机辅助工艺过程设计(CAPP)、计算机辅助工程(CAE)和计算机辅助制造(CAM)等;包括信息化水平,如企业信息化系统中的制造资源计划(MRP)、企业资源规划(ERP)和生命周期管理(PLM)等;还包括生产线布局优化水平和单元化柔性制造水平等要素。
专业能力则是基于航天技术专业和产品特点所形成的个性化制造能力,航天装备制造过程涉及大型、异型复杂结构件加工和成形,微、精、专器件的生产制造,复合材料加工和制造等不同领域;涉及机械加工、焊接、成形、铸造、热处理等不同专业以及相关的专业测试与检验技术等。这些专业能力若存在短板或瓶颈将会直接影响航天装备制造系统的运行效率和效益。
管理能力包含外部体制机制和内部管控规程两个方面。外部体制机制主要指航天装备制造的外部政策环境、国家投入力度、保障手段等方面;内部管控规程主要指航天装备制造系统内部的运行机制,包括计划调度、协作配套、考核评价等。
三、航天装备制造的发展趋势
(一)航天装备极端制造的特征越来越明显
极端制造是指在极端条件或环境下,制造极端尺度或极高功能的产品、器件和系统。随着人类的航天活动由近地迈向深空、由无人转向有人,航天装备越来越多地表现出极端制造的特征。
大型化和重型化:空间基础设施建设呈现出大型化和重型化的趋势,如空间站需要分阶段在空间组装建设,大容量卫星需要大型卫星平台支持,重型运载火箭需要大部段结构制造,为适应一星多用、长寿命运行的发展要求,卫星所携带的有效载荷和燃料越来越多,越来越重。
精密化和小型化:航天装备结构形状与零部件配合关系复杂,其对尺寸精度、表面质量以及装配精度要求很高,如卫星的仪表轴承的圆度、圆柱度、表面粗糙度等均要达到纳米级。同时,高性能的微小航天器的设计与制造,如微传感器、微控制器、微能源、微光学器件等对航天装备制造提出了新的要求和挑战。
高性能和独特性:航天制造面临很多独特的需求和问题,如特种工艺、特种材料等,航天产品的关键零部件如框、梁、接头、壳段等大量使用钛合金、高强度及高温合金钢、工程陶瓷等难加工材料。同时,由于订货量小、用量少,往往还面临供货不连续和生产线难以维持的问题,因此特别需要各个工业部门的协同配合。
(二)航天装备制造正向数字化、网络化、高可靠性、低成本、高效率方向发展
1. 数字化
以美国国家航空航天局、美国波音航空航天公司、法国空中客车公司、美国洛克希德·马丁空间系统公司等知名研究机构和企业为代表,国外航天制造业通过数字化设计制造手段实现了产品质量、协同效率、研制能力的大幅度提升。2014年美国宣布在芝加哥设立公私合营的“数字制造与设计创新研究所”,可快速实现计算机设计和工程原型研制,以更加先进的制造技术实现复杂的设计,使美国国家航空航天局在建造、测试和试飞下一代空天系统的过程中速度更快、效费比更高。
2. 网络化
国外主要航天承包商已普遍实现了网络化的协同设计与制造,美国国家航空航天局开展了智能化综合工程环境(intelligent synthesis environment, ISE)的研究工作,将高性能计算机、高速网络、数字化产品与基于知识的设计、人工智能、人机交互技术有效地结合在一起,形成了一种跨地域的虚拟协同环境,不同地域、身份和学科的专家和工程技术人员在此平台上进行综合设计和航天产品设计、试验和样机制造,提高了卫星研制效率,节省了研制成本。
3. 高可靠性
随着空间探索向更远、更深的领域延伸,特别是载人登月、火星探测等深空探测工程项目的实施,对航天装备的可靠性提出了更为严苛的要求。美国国家航空航天局在《2014年战略规划报告(NASA Strategic Plan 2014)》中指出其正致力于克服空间辐射、后勤保障和长时可靠性等挑战,对航天高可靠性问题给予了高度重视。
4. 低成本
国外航天承包商积极推动低成本制造技术,一方面通过基于成本的设计、并行工程、集成产品开发、数字化设计、网络化制造、建模仿真等技术手段,从设计源头、研制流程和研制环境等方面降低制造成本;另一方面,大力发展卫星平台、微小卫星、可重复使用运载器等航天技术降低航天任务成本。此外,还通过商业化模式实施精益生产来大幅降低成本。
5.高效率
为了提升效率、缩短交付周期,美国提出了“精益飞机研制计划(Lean Aerospace Initiative, LAI)”。该倡议来源于一个以麻省理工学院为领导的包含政府机构、航空航天军工企业的组织,其目标是帮助航空航天工业界实现以更少的时间、更低的成本交付质量更高的产品。同时,一些商业化的航天企业在提高效率方面也取得了显著的进展,如美国太空探索技术公司(SpaceX)的猎鹰9号火箭从一无所有到实现首飞只用了4年半的时间,而其载人“龙飞船”(Crew Dragon)从一无所有到实现首次验证飞行只用了4年时间。
(三)航天先进制造技术快速发展,应用范围不断扩大
国外航天制造业在先进成形技术、先进连接技术、复合材料制造技术以及数字化制造技术与装备方面得到了进一步提高,涌现出一批新的制造工艺与技术,如美国国家航空航天局联合洛克希德·马丁空间系统公司研制出了推进剂贮箱整体成型技术,可省去大量的焊接与检验步骤;美国波音航空航天公司、法国空中客车公司、洛克希德·马丁空间系统公司应用数字化装配技术、虚拟实验室等先进数字化制造技术缩短加工周期,降低制造成本。空间在轨装配和航天增材制造(3D打印)技术正在成为广受关注的重点领域。美国国家航空航天局实施了具有改变游戏规则意义的大型结构系统太空装配项目,美国国防部先进研究项目局(DARPA)授予美国劳拉空间系统公司(SS/L)一项研究地球静止轨道通信卫星在轨机器人组装技术(“蜻蜓”项目)的合同。雷神公司、洛克希德·马丁空间系统公司、法国空中客车公司等航天企业集团都开展了3D打印技术在火箭、导弹、卫星等领域的应用研究,均取得了较好的效果。
四、我国航天装备制造的现状与问题
航天装备制造作为我国航天科技工业体系的坚强基石和核心能力,是我国航天可持续发展的基础,先进的工艺技术和制造能力是确保各项科研生产任务顺利完成的重要保障。
近年来,我国航天装备制造的技术水平随着型号任务的开展取得了显著提升,突破了新一代运载火箭大型贮箱制造装配工艺和以焊接铣切一体化大型焊接装备为代表的一大批关键技术,普遍实施了以产品为中心来替代以专业分工为中心进行生产单元组建的生产方式,加快制造工艺与装备的升级换代,大量引进并应用了工艺管理系统、生产派工系统、车间制造执行系统等信息化平台,在三维数字样机开发、设计工艺协同、工艺设计仿真验证等方面取得了一定突破,航天装备制造逐步开始向数字化研制模式过渡与转型。
当前,西方发达国家重新认识到了制造业的地位和价值,力争要在新一轮先进制造业竞争中取得优势地位;我国航天装备制造技术水平与国外航天先进水平相比还有一定差距,还不能很好地适应航天产业快速发展的要求。
(一)适应航天装备特点的制造模式仍处于摸索、调整阶段
我国航天装备制造主要采用研制与批量生产混合共线的模式,其批量生产能力不强。在研制和批量生产模式发生冲突时,批量生产能力易受到影响。同时,由于航天产品多品种、小批量的特点,使其制造过程换型频繁,再加上缺乏在线原位检测设备和快装快换的工具手段,使得制造单元的制造效率难以获得根本性的提升。
航天装备制造数控化水平比较低,劳动密集型的手工生产模式普遍存在。设计—工艺—现场生产线之间的数据链路没有贯通,设计阶段生成的数字化模型无法直接辅助生产制造。工艺仿真、数字化装配等先进数字化制造技术能力薄弱。
设计制造一体化程度不高。工艺设计与产品设计尚未实现并行工程,工艺提前介入设计的程度有限,导致设计方案的可制造性不强。设计与工艺之间的系统平台、专业软件、标注规范尚不统一,设计模型和数据难以共享。
(二)工艺手段落后,对先进工艺方法积累不充分
我国对工艺在航天科研生产体系中的作用重视不够。长期以来,我国航天制造业一直是通过研制来建立科研生产体系的,出现了重科研轻生产,重设计轻工艺的现象,对工艺在科研生产中的作用认识不足,重视不够,没有建立独立、完善的工艺发展体系,难以从根本上提高工艺的技术水平和能力,制约了我国航天装备制造能力的进一步提高。
工艺技术水平尚不适应型号任务快速发展的要求。在航天型号研制生产过程中,随着新技术、新设备、新材料的大量应用,客观上要求加大工艺攻关力度以适应型号任务需要;但从整体上看,我国航天工艺技术研究欠缺,创新不足,一些新型号的研制仍然沿用几十年前的工艺方法,难以适应型号任务的发展要求。
工艺手段较为陈旧。对先进工艺技术手段的应用不够,相较于计算机辅助设计和计算机辅助制造环节,工艺环节的计算机辅助工艺过程设计成为了航天数字化制造模式的短板。先进工艺手段的缺乏使得工艺规程的一致性较差,效率较低,同时,工艺标准、工艺技术成果也难以进行有效的积累、管理和复用。
(三)我国航天装备制造的专业能力亟待提升
航天大型、异形复杂结构件的制造能力还不能满足型号研制需求。随着国家航天活动由近地向深空、由单一任务向多任务、由短期停留向长期驻留的扩展,航天装备的结构尺寸和结构复杂程度大大增加,这对我国大型、异形复杂结构件的加工和成型能力提出了更高要求;因此,面向未来的航天型号任务,亟需研究能够突破大结构尺寸产品和异形结构产品的装配技术、测量技术、大直径运载火箭贮箱原位制造基础技术和大型铆接筒段壳体自动化铆接成套装备、贮箱箱底整体旋压装备、大型铝合金环形结构件精确校形装备等。
航天精密制造能力有待进一步提升。目前,以生产惯性器件、微电子、光学遥感器为代表的航天精密、超精密制造技术已由宏观制造领域进入微观制造领域,精度要求已经达到了亚微米,甚至纳米级,这对我国航天装备制造业的精密加工、精密成型、精确装配等精密制造技术提出了更高要求。我国现有的航天装备技术水平距离精密制造技术还有一定差距,比如我国新一代高精度惯性仪表和平台系统在设计技术和指标上能够接近国际先进水平,但其关键零部件的精密制造技术水平低,工艺装备落后,导致其研制周期长,制造成本高,产品精度和可靠性低,产品质量和批量生产能力难以进一步提高。
航天复合材料制造能力与国外先进水平相比还存在一定差距。随着航天任务要求越来越高,航天高性能复合材料的用量也在迅速扩大,各种航天飞行器的重要结构件,如运载火箭和导弹的壳体、飞船部件、卫星天线等的生产,正在越来越多地采用复合材料,这对我国航天复合材料的制造技术水平和制造能力提出了更高要求。我国航天制造业在铝锂合金等新型轻质材料及钛合金等高熔点合金的成型、连接及增材制造技术,热防护材料、高模量碳纤维、耐烧蚀纤维陶瓷等先进功能复合材料技术与自动成型加工装备等方面与国外先进水平相比还有一定差距。
(四)管理机制仍不能完全适应我国航天装备制造发展的需要
航天装备制造企业所获得的投入和支持力度相对不足。我国航天生产制造企业在整个航天科技工业体系中话语权较小,所获得的资源投入相对较少。国家军工固定资产投资型号痕迹过重,锻造、铸造、焊接、检测等航天基础制造能力获得的投入较少。航天生产制造企业往往面对多家设计单位,同时承担多个型号的研制与批量生产任务,普遍面临着制造资源紧张、人员加班加点的问题。
航天装备制造系统中不同单位间的协同性有待加强。航天设计单位与制造单位相互分离,协同性不高,设计单位与工艺单位之间缺少沟通,技术状态变更频繁,制造工艺难以稳定。主管单位与分系统单位、上下游单位之间的计划调度安排不够合理,制造资源占用均衡性、进度匹配性较差,产品难以齐套;前方与后方制造企业之间存在转接产技术交底不充分的现象,造成后期多次沟通协调、重复投入资源开展工艺攻关等问题。
科研管理难以有效支撑航天装备制造能力的提升。在长期保成功的压力下,为达到航天产品高可靠性的要求,航天装备制造在采用新技术、新工艺方面较为保守,只有在其他型号上应用成功后才敢使用,先进的制造技术、工艺转化推广较慢。航天装备产品化程度较低,距离通用化、系列化、组合化的“三化”要求还有一定差距,制造效率难以提升。
五、对策建议
随着国家重大科技专项和重大航天工程的实施,多型卫星、航天器进入批量研制和生产阶段,亟需立足自主可控,加强系统谋划,进一步优化制造资源配置,解决关键瓶颈和短线问题,大力提升我国航天装备制造能力,实现航天事业可持续发展。
(一)着眼先进理念,全力推进先进制造模式
开展数字化模型的规范化和标准化专项工程,统一和规范设计、制造上下游数字化模型的平台、软件的生成与标识方案,实现数字化模型上下游间的贯通。积极探索航天系统工程创新发展,实现基于模型的航天装备的开发制造过程,大力推行集成产品开发方法,实现航天装备设计制造一体化;构建航天协同设计工程环境、航天装备制造系统、企业资源规划系统集成交互的制造模式,实现航天装备制造的数字化、网络化和集成化。
(二)强化工艺创新,大力提升工艺技术能力
加强对航天工艺技术发展的系统规划,完善工艺创新的激励机制,加快工艺创新成果的工程化应用。推行工艺先行于设计进行先期攻关突破的工艺研发方式,提前进行工艺储备,达到工艺拉动设计,技术推动设计的目的。开展计算机辅助工艺过程设计技术的应用示范工程,加大对工艺路线、流程、方法及相关软件、工具的支持力度,充分发挥工艺在航天制造系统中的枢纽作用,实现设计–工艺–制造的一体化集成。
(三)围绕航天工程实际需求,攻关突破瓶颈环节
围绕月球探测、高分辨率对地观测系统、载人航天、北斗导航等重大航天工程的实际需求,加强对难以引进的航天高端专用制造装备研制的投入力度;针对短板和瓶颈问题,系统谋划,加强攻关,重点解决生产关键元器件精密/超精密制造装备、先进功能性复合材料制造装备、大型复杂异形结构制造装备、自动化柔性对接装配装备、先进检测设备等长期制约我国航天制造能力的瓶颈环节。
(四)加强人才队伍建设,为航天装备制造提供有力的人才保障
积极借鉴培养航天型号研制队伍的成功经验,探索建立航天能力建设总设计师、航天型号生产总指挥的人才队伍体系,强化设计–工艺–现场的综合人才培养,扩展航天工艺制造专业人员培养和成长的通道,加速培养航天制造能力建设、型号批量生产的高端领军人才,大力推行集成产品团队模式,切实发挥工艺人员在设计和现场之间进行有序、有效衔接的桥梁作用。
(五)推动管理变革,构建促进航天装备制造发展的有利环境
加强资源整合,建设军民协同、国家大协作条件下的自主和可持续发展的航天制造系统,提升对核心、高端航天制造环节的自主可控力度,同时对一般的航天制造环节要积极引入社会制造资源,提升效率,降低成本;完善国家航天能力建设布局,加强统筹协调,加强对铸造、锻造、热处理等航天制造基础能力的投入力度;成立航天制造系统专业研究机构,主要负责航天制造系统的共性技术探索和相关标准制定,开展航天先进制造技术发展战略研究,围绕增材制造、数字化制造、智能制造等领域开展先进制造技术预先研究,为建立适应我国当前航天任务需要和未来航天能力发展需要的航天制造系统提供全面支撑。
六、结语
航天装备是我国空间基础设施和卫星应用产业发展的物质基础,航天装备制造具有极高的复杂性和特殊性。当前,我国航天先进制造模式和技术发展迅速,航天型号任务对航天装备制造能力提出了更高要求,亟需针对我国航天装备制造存在的短板和瓶颈问题,通过构建先进的航天制造模式,强化工艺创新,突破航天制造装备技术瓶颈,强化人才队伍建设和营造有利的发展环境等举措,实现我国航天装备制造能力跨越式发展,推动我国航天强国的建设。
注:本文内容呈现略有调整,若需可查看原文。
作者介绍
栾恩杰,导弹控制技术和航天工程管理专家,中国工程院院士。
参与组织、主持首型潜地战略导弹和首型陆基机动中程战略导弹研制,提出陆基机动中程战略导弹型谱化、系列化发展思路,适应了发展需求。参与组织、主持首次月球探测工程,提出深空探测“探、登、驻(住)”和“绕、落、回”的技术发展路线,开辟了深空探测新领域。在航天型号和工程研制工作中取得了一系列开拓性和创新性成果,为我国武器装备和航天事业发展做出重大贡献。在长期工程实践中,提出了适合国情的系统工程管理理论与方法,已广泛应用于国防科技工业系统并取得显著效果。
本文来自微信公众号:中国工程院院刊(ID:CAE-Engineering),作者:《中国工程科学》